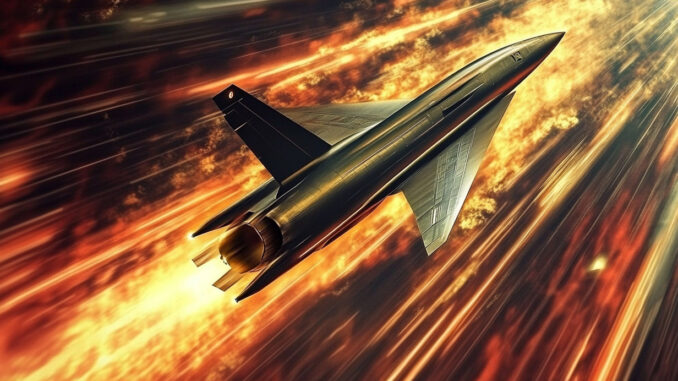
Hypersonic technologies require advances in materials and aerodynamics to cope with extreme thermal and mechanical constraints.
Hypersonic speed, in excess of Mach 5 (approximately 6,174 km/h), represents an immense technical challenge because of the thermal, aerodynamic and mechanical forces it imposes on vehicles. At this speed, the temperature of materials can reach over 2,000°C, making the development of new heat-resistant materials essential. At the same time, the management of airflow and turbulence becomes crucial to maintaining vehicle stability. Propulsion technologies, such as ramjets, are also essential to enable continuous flight at these speeds. This article presents the main technical challenges encountered in the development of hypersonic systems.
Thermal constraints at hypersonic speeds
When a vehicle reaches hypersonic speed, the friction between its surface and the air molecules generates intense heat. At Mach 5, surface temperatures can exceed 2,000°C, which is beyond the capabilities of traditional materials. Engineers must therefore use ceramic and composite materials capable of withstanding these temperatures without deteriorating. Although these materials are resistant, they remain expensive, and their use in complex structures poses a number of industrial challenges.
In addition, at hypersonic speeds, the heat is not distributed uniformly. Certain areas, such as the nose of the aircraft and the leading edges of the wings, can experience higher temperatures. It is therefore essential to design localised thermal protection systems. NASA, for example, has developed a heat shield made of ceramic tiles to protect its spacecraft during atmospheric re-entry phases at similar speeds. These technologies are necessary to maintain the integrity of the structures and avoid irreversible damage to the vehicle.
Finally, it should be noted that materials exposed to such high temperatures must also withstand intense thermal cycles during acceleration and deceleration. This creates another challenge: ensuring the durability of the materials in the face of these variations, by limiting the risks of cracks and mechanical fatigue.
Managing aerodynamic flows
Air flows at hypersonic speeds pose major challenges for vehicle stability and handling. At Mach 5 and above, shock waves form around the aircraft, considerably altering its aerodynamic properties. This leads to extreme turbulence and pressure variations, which must be anticipated to ensure safe and efficient flight.
The shockwave generated at the front of the aircraft causes rapid compression of the air, increasing the pressure and temperature of the air around the vehicle. This phenomenon, known as shock bow, is particularly complex to model. Engineers have to use supercomputers to simulate these interactions in real time and optimise the aerodynamic shape of the vehicle. In terms of design, hypersonic vehicles often have a tapered profile and thin leading edges to reduce air resistance and mitigate the effects of shock waves.
In addition, control surfaces (ailerons, rudders) lose their effectiveness at these speeds. Active control of airflow therefore becomes essential to maintain trajectory. This requires the integration of advanced flight control systems and materials capable of withstanding mechanical and thermal forces. DARPA, for example, is working on hypersonic flight technologies that incorporate adaptive systems to adjust control surfaces according to real-time conditions.
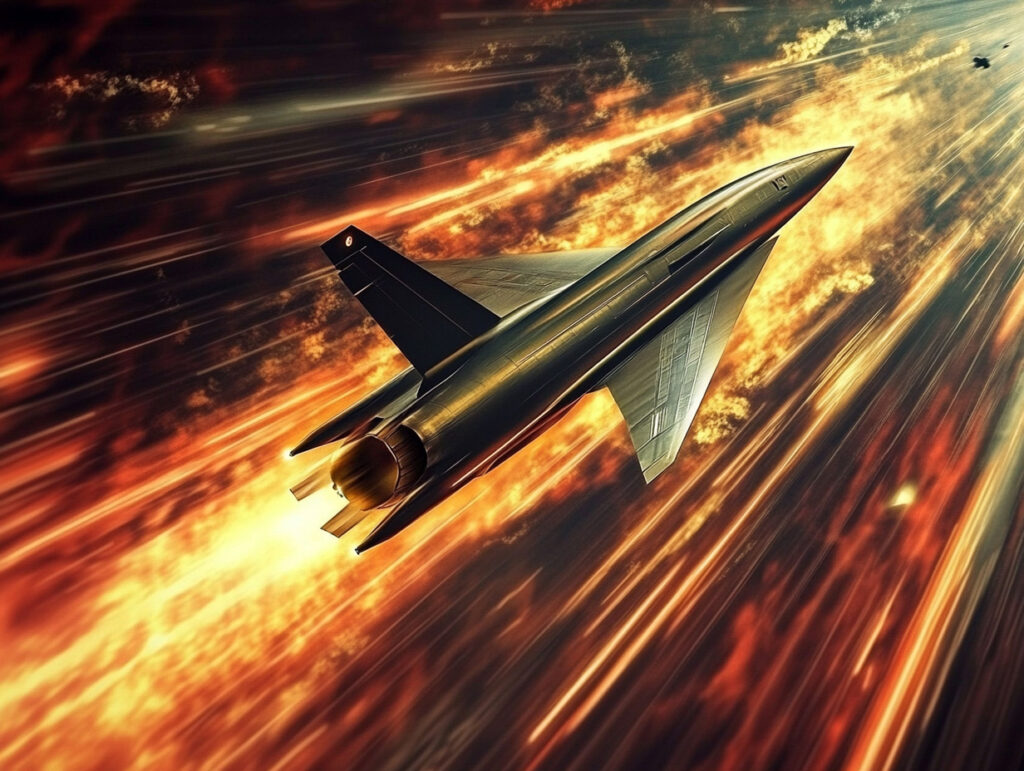
The challenges of hypersonic propulsion
One of the most complex aspects of hypersonic flight is propulsion. At these speeds, traditional engines, such as turbojets, are not sufficient. Technologies such as the supersonic combustion ramjet (or scramjet) are being considered to provide continuous propulsion. The scramjet uses oxygen from the atmosphere as an oxidant, eliminating the need for the oxygen tanks used in traditional rocket engines.
However, designing an efficient scramjet is extremely difficult. Air must be compressed at hypersonic speeds while being introduced into the combustion chamber at subsonic speed. This compression process generates extreme pressures and temperatures, making combustion control tricky. Poor compression management can lead to thermal shock and loss of efficiency.
Prototypes developed, such as Boeing’s X-51 Waverider, have shown that scramjet propulsion is possible, but flights only last a few minutes. One of the challenges is to guarantee stable combustion and increase the duration of hypersonic flights while reducing fuel consumption. Heat-resistant materials must also be used in the combustion chamber to withstand the high temperatures generated by the rapid combustion of air and fuel.
Impact on vehicle structural design
The structural design of hypersonic vehicles must take into account a number of technical factors. In addition to thermal and aerodynamic constraints, the mechanical forces imposed on the structure are immense. The pressure exerted on the device can reach several megapascals (MPa), making the strength of the materials crucial.
Structures must be both lightweight and extremely robust to withstand these stresses. The development of new alloys and composites is therefore essential. For example, titanium and carbon are often used for their strength and lightness properties. However, the cost of these materials is high, with prices approaching €50 per kilogram for aerospace-grade titanium.
As well as strength, the flexibility of materials is another key parameter. During hypersonic flight, significant vibrations and oscillations can occur due to pressure variations and turbulence. Materials must be able to absorb these vibrations without cracking or deforming.
The strategic and industrial consequences of mastering hypersonic flight
Mastering hypersonic flight presents major strategic challenges for nations investing in these technologies. Hypersonic speed considerably reduces reaction time for military strikes, particularly against targets thousands of kilometres away. For example, a hypersonic missile could reach a target 3,000 km away in less than 30 minutes, reducing the ability of defence systems to intercept such missiles.
The aerospace industry is also positioning itself in this promising market. Companies such as Lockheed Martin and Boeing are investing heavily in research to develop hypersonic aircraft and missiles, estimating that the market will be worth several billion euros over the next few decades. The development of these technologies also represents opportunities in the civil sector, particularly for ultra-fast transcontinental flights.
However, development costs remain very high. Tests in hypersonic wind tunnels and flight tests require specialised infrastructures, with budgets in excess of €100 million per programme. This financial barrier limits access to these technologies to a small number of countries and companies.
War Wings Daily is an independant magazine.