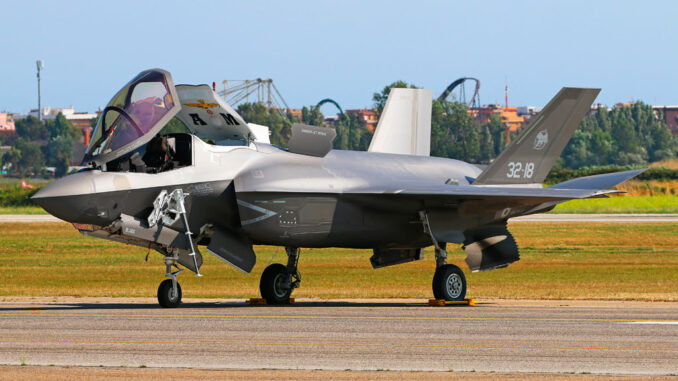
Reduce the cost of fighter aircraft development through appropriate design, digital tools and targeted cooperation.
Fighter aircraft development is notoriously expensive. This covers fighter aircraft design, prototyping, testing and industrialization. Recent programs, such as the F-35 and Rafale, have shown that fighter aircraft development can easily run into tens of billions of euros. This is due to the technical complexity of the project, the level of integration of multiple advanced systems, and the numerous regulatory and operational constraints.
The question of how to reduce these development costs is now central. Managers are looking for clear and concrete methods to better control the entire process. Objectives include reducing the time spent on testing phases, improving robustness right from the design stage, and rationalizing components and materials. Approaches already exist, such as the use of numerical tools, more comprehensive simulations, and greater standardization of certain parts. Other approaches include broader industrial agreements, a more balanced distribution of workloads, and the adoption of new procurement methods.
The aim is to achieve a lasting balance between performance, quality and budgetary control. The development of fighter aircraft must be based on more economical approaches, without compromising operational requirements. The sectors involved are considering the best way to proceed, while taking into account external constraints such as the pace of technological change, competitive pressures and defense policies. A number of avenues are being explored, paving the way for an overhaul of practices.
Context of development costs in fighter aircraft design
Analysis of amounts invested
The development cost of a fighter aircraft often runs into tens of billions of euros. The F-35 program, initiated by Lockheed Martin, illustrates this phenomenon. According to various estimates, initial development, including research and prototyping, exceeded 50 billion euros. The Rafale program, designed by Dassault Aviation, also has a similar budget level for the design and engineering phase. These amounts cover the integration of complex equipment, flight testing, certification and progressive industrialization.
Regulatory and operational requirements
Complying with international standards and obtaining certification requires a series of tests and validations. Each additional requirement lengthens the timetable and increases the total cost. For example, the integration of an AESA (Active Electronically Scanned Array) radar requires meticulous testing, including performance evaluation in various atmospheric conditions. The incorporation of composite materials, which are lighter than steel, also requires specific validations. Every regulatory or operational constraint requires an extensive technical review, adjustment and control.
Competitive pressure and strategic challenges
The design of a fighter aircraft takes place in a competitive context, with players seeking to gain a technological advantage. This competition drives the integration of advanced weapons systems, encrypted communication systems and adaptive sensors. Initial objectives are frequently exceeded when additional functionalities are added along the way, creating the need for re-engineering and new test campaigns. This dynamic increases overall costs, and prompts each player to keep a close eye on technology choices, subcontracts and schedules.
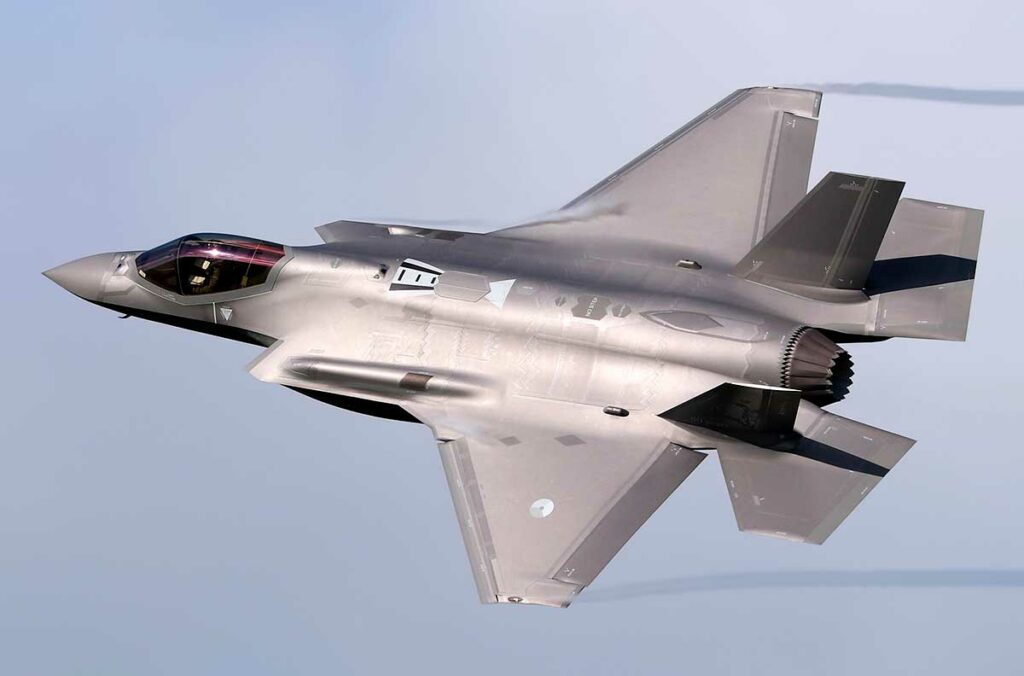
Streamlining R&D processes
Reducing actual test phases through simulation
Numerical simulation reduces the number of real-life tests. Software such as Ansys or Siemens Simcenter assess lift, drag or aerodynamic stability. This approach reduces the need for costly prototypes. For example, simulating the behavior of a specific composite material reduces the need to manufacture several parts to validate its properties. What’s more, fitting an aerodynamic profile to a virtual model enables behavior to be verified at different speeds, from 0 to 2,000 km/h, without the need for lengthy flight test campaigns. This method generates significant cost savings, often estimated at several hundred million euros.
Improving robustness right from the design phase
Integrating finite element analysis (FEA) and computer-aided design (CAD) tools at an early stage helps to anticipate structural constraints. Engineers check the strength of the wings by simulating loads of several tens of kN. In this way, they fine-tune the distribution of forces on the structure, reducing the need for subsequent corrections. This reduces the need for intervention on physical prototypes, and cuts overall development time.
Optimizing component life cycles
Analyzing the projected lifetime of parts right from the design stage ensures better prediction of overall cost. Data on fatigue, corrosion or wear resistance of critical components can be used to select specific alloys and establish an optimized inspection schedule. A simple adaptation of a bearing’s material, with a 20% longer life, limits the need for replacement over the long term. This approach reduces the maintenance bill and ensures more accurate budget monitoring over the entire operating life.
Standardization and modularity of parts
Adoption of interchangeable components
The adoption of standardized components encourages reuse on different models. For example, a generic hydraulic system can be installed on several versions of a machine. This reduces development costs, as only one design and validation process is required. A fuel tank designed for one model can be adapted, with a few adjustments, to another, without the need for a complete new R&D cycle. This method limits the need to manufacture specific parts, which are often more costly, and reduces overall design time.
Simplified maintenance and logistics
Modular components facilitate maintenance, as the workshop can quickly replace a part without having to stock a large quantity of different parts. A standard electronic unit eliminates the need to acquire large stocks. This simplification improves availability and reliability, while limiting storage costs. For example, a universal electronic module costs around EUR 100,000, whereas a specific equivalent, designed only for a particular model, can cost upwards of EUR 200,000.
Reduced dependence on specific suppliers
The use of interchangeable materials reduces dependence on a single supplier. This flexibility makes it possible to negotiate prices and delivery times. A generic component, produced by several manufacturers, offers lower prices than an exclusive part. For example, a generic servo motor, available from several suppliers, can cost around EUR 50,000, compared with over EUR 80,000 for an exclusive equivalent. This approach supports budgetary control and secures supply.
Digital tools and virtual engineering
Upstream performance simulation
The use of simulation software such as ANSYS or Dassault Systèmes SIMULIA facilitates the prediction of loads, material resistance and aerodynamics prior to production. Simulating airflow at 2,000 km/h enables you to adjust the profile of a wing without creating a physical prototype. This practice, which is often billed at around 500,000 EUR for a series of analyses, can save several million EUR in costs associated with actual wind tunnel testing. This approach also reduces the duration of on-site test campaigns and limits late modifications.
Virtual prototyping and digital mock-ups
3D modeling tools offer the possibility of creating a complete model in a virtual environment. This representation shows the geometry, internal layout and interfaces between various systems. An engineer can, for example, check the location of a 500 L tank and identify an assembly constraint at an early stage. This limits the need for physical prototypes, which can cost tens of millions of euros. By detecting errors earlier, it avoids complex subsequent corrections.
Integrated technical data management
PDM (Product Data Management) or PLM (Product Lifecycle Management)** systems centralize all design-related data. Drawings, 3D models, specifications and configurations remain accessible on a single platform. This integration simplifies coordination between teams, reduces inconsistencies and prevents unnecessary purchases. For example, a EUR 30,000 sensor can be quickly identified, avoiding unnecessary orders. Consistently organized technical data reduces wasted time and redundant modifications.
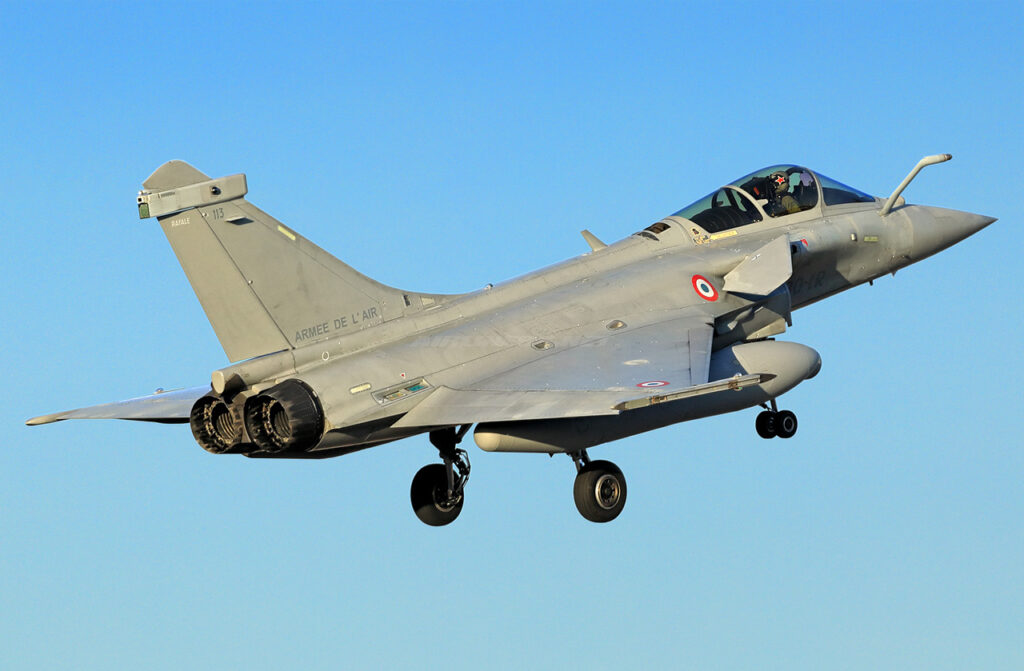
Industrial partnerships and international cooperation
Sharing costs between several players
A program involving several participants enables the financial burden to be spread over several national or industrial budgets. For example, the Eurofighter Typhoon program, shared between the UK, Germany, Italy and Spain, has enabled investments estimated at over 50 billion euros to be pooled. This approach limits dependence on a single player and reduces the unit cost per aircraft. By sharing the burden of R&D, flight testing and production, no single player has to bear the entire cost.
Know-how transfer and skills consolidation
An international partnership facilitates the exchange of knowledge and methods. One company with expertise in aerodynamics works with another specializing in on-board electronics. This interaction accelerates development, as each team avoids investing years in acquiring skills already available elsewhere. For example, a French research center collaborating with a German laboratory reduces the time needed to develop an active antenna radar. Sharing test data, accessing proven technologies and optimizing in-house training reduce the risk of errors and delays.
Agreements to promote technical synergies
Formal agreements between players define roles and responsibilities, as well as timetables. A clear contract, a coherent work plan and precise technical milestones ensure efficient organization. For example, one group defined for propulsion, another for fuselage and a third for avionics. This rational segmentation limits redundancies and reduces the risk of additional costs. The aim is to make each subsystem compatible, limit rework and validate performance within a controlled timeframe. This method helps to stabilize the overall budget and to deliver a device that meets operational requirements more quickly.
Procurement, supply chain and cost control
Rigorous supplier selection
Precise analysis of suppliers ensures consistent quality and controlled lead times. For example, the use of a single partner specializing in the manufacture of light-alloy components, invoiced at around EUR 200,000 per batch of 10 parts, reduces the risk of defects. This strategy offers long-term stability and limits delivery delays. Assessment of technical capabilities, quality track record and pricing conditions minimizes last-minute adjustments.
Anticipatory supply chain management
Advanced component flow planning reduces storage costs and avoids assembly interruptions. A coordinated supply schedule with subcontractors ensures that parts are available at the right time. For example, scheduling the receipt of hydraulic systems 2 weeks before their integration avoids warehouse bottlenecks. Computerized stock tracking, via ERP (Enterprise Resource Planning) software, guarantees reliable availability and visibility on quantities, lead times and costs, estimated at between EUR 50,000 and EUR 100,000 per year in software and maintenance.
Setting up precise budget monitoring indicators
Numerical indicators, such as unit cost per module, maintenance margin over 5 years, or defect rate per batch, enable strict management. Monthly monitoring of expenditure, with a dashboard including a margin of error of less than 5%, quickly signals an abnormal rise in costs. Thanks to consolidated data, management can identify deviations and adjust the procurement plan, ensuring overall budget stability.
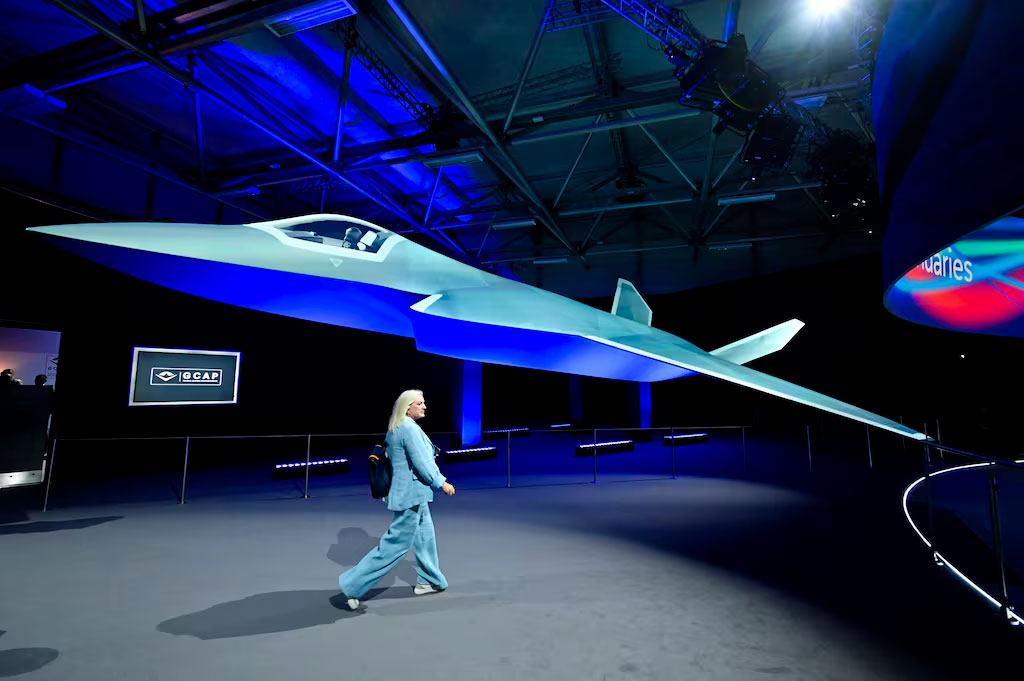
Continuous improvement and prospects
Adapting to technological change
Constant technological monitoring enables us to anticipate the integration of higher-performance, lower-cost components. For example, a recently miniaturized radar sensor costing EUR 150,000 improves accuracy without increasing total cost. Keeping abreast of advances in materials, electronics and propulsion means we can regularly update the options available.
Team training and in-house skills development
Upgrading in-house skills through technical training helps anticipate future needs. For example, a technician trained in alloy laser welding reduces the need for an external service provider, saving nearly 40,000 euros over a maintenance cycle. Targeted training plans, invoiced at between EUR 10,000 and 20,000 per session, create a pool of know-how directly available on site.
Incentives for innovation and profitability
Flexible contracts with partners encourage the search for more cost-effective solutions. A 5% bonus granted to a supplier who delivers a part 10% cheaper encourages innovation. This approach encourages the proposal of new technologies or more efficient production methods, limiting long-term cost increases and stabilizing the overall budget.
War Wings Daily is an independant magazine.