Experimental aircraft with ultrathin, strut-braced wings aiming to reduce fuel consumption and emissions by up to 30% for sustainable aviation.
The NASA-Boeing X-66A is an experimental aircraft developed to demonstrate the Transonic Truss-Braced Wing (TTBW) configuration. This design features ultrathin wings supported by diagonal struts, aiming to enhance aerodynamic efficiency. The aircraft is a modified McDonnell Douglas MD-90, incorporating advanced propulsion systems and materials. With a wingspan of 145 feet (44.2 meters), the X-66A is designed to cruise at speeds up to Mach 0.80. The project seeks to achieve a 30% reduction in fuel consumption and emissions compared to current single-aisle aircraft, contributing to the goal of net-zero aviation greenhouse gas emissions by 2050. Flight testing is scheduled to commence in 2028.
History of the Development of the NASA-Boeing X-66A TTBW
In the early 21st century, the aviation industry faced mounting pressure to address environmental concerns, particularly the reduction of greenhouse gas emissions. Single-aisle aircraft, which constitute a significant portion of the global fleet, were identified as key targets for efficiency improvements. In response, NASA initiated the Subsonic Ultra Green Aircraft Research (SUGAR) program in 2010, exploring innovative aircraft configurations to enhance fuel efficiency and reduce emissions.
Boeing, as a principal collaborator in the SUGAR program, investigated various design concepts, leading to the development of the Transonic Truss-Braced Wing (TTBW) configuration. This design features ultrathin, elongated wings supported by diagonal struts, aiming to reduce aerodynamic drag and improve fuel efficiency. Extensive wind tunnel testing at NASA’s Ames Research Center in 2019 validated the potential of the TTBW design, demonstrating the feasibility of cruising at speeds up to Mach 0.80, comparable to contemporary jetliners.
Building upon these promising results, NASA and Boeing launched the Sustainable Flight Demonstrator (SFD) project in January 2023. The project’s objective is to construct and test a full-scale demonstrator aircraft embodying the TTBW design. The U.S. Air Force designated this experimental aircraft as the X-66A in June 2023, marking it as the first X-plane focused on achieving net-zero aviation greenhouse gas emissions.
To develop the X-66A, Boeing selected a McDonnell Douglas MD-90 airframe for modification. In August 2023, the MD-90 was ferried to Boeing’s facility in Palmdale, California, where it underwent significant structural alterations. These modifications included removing the original wings and engines to accommodate the new TTBW configuration. Advanced 3D metrology scans were employed to inform the precise integration of new components, ensuring structural integrity and aerodynamic performance.
The X-66A project represents a collaborative effort involving multiple stakeholders. In July 2023, major U.S. airlines—including Alaska Airlines, American Airlines, Delta Air Lines, Southwest Airlines, and United Airlines—joined a sustainability coalition to provide operational insights. Their feedback focuses on design considerations, maintenance practices, handling characteristics, and airport compatibility, ensuring the demonstrator aligns with real-world operational requirements.
The development timeline anticipates ground and flight testing to commence in 2028 at NASA’s Armstrong Flight Research Center, located at Edwards Air Force Base. The insights gained from the X-66A’s testing phase are expected to inform the design of next-generation single-aisle aircraft, contributing significantly to the aviation industry’s environmental sustainability goals.
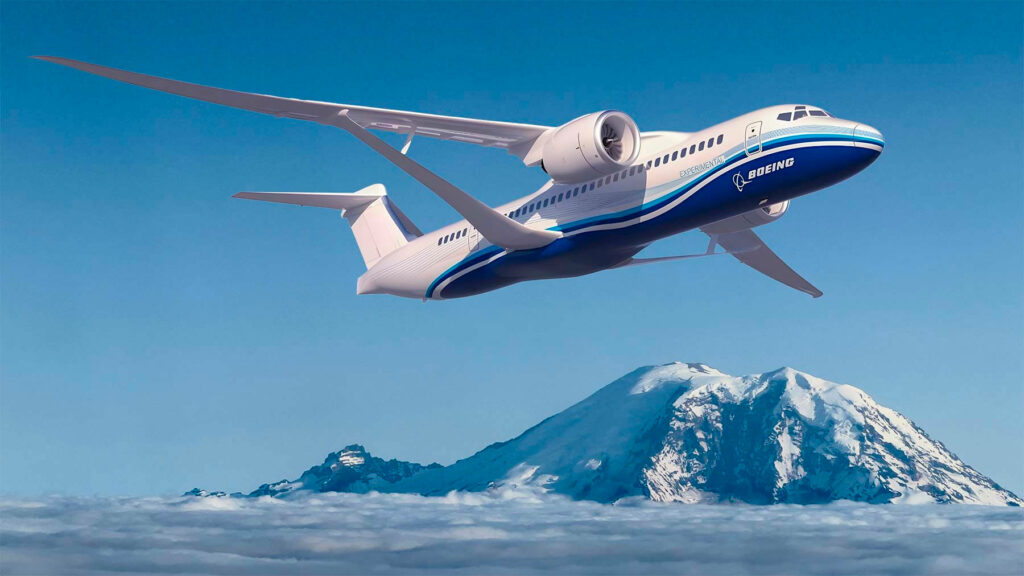
Design of the NASA-Boeing X-66A TTBW
The NASA-Boeing X-66A’s design centers on the Transonic Truss-Braced Wing (TTBW) configuration, a departure from traditional cantilever wing structures. This innovative design features ultrathin wings with an extended wingspan of 145 feet (44.2 meters), significantly longer than those of conventional single-aisle aircraft. The wings are supported by diagonal struts, or trusses, that connect the wings to the fuselage, providing additional structural support and allowing for a higher aspect ratio.
The high aspect ratio of the wings reduces induced drag, enhancing aerodynamic efficiency and contributing to lower fuel consumption. The ultrathin profile of the wings further minimizes drag, enabling the aircraft to achieve cruise speeds up to Mach 0.80. This performance is comparable to current jetliners, ensuring compatibility with existing flight operations.
Structurally, the integration of diagonal struts allows for the extended wingspan without a significant weight penalty. The truss system effectively distributes aerodynamic loads, reducing bending moments on the wing and permitting a lighter wing structure. This design approach not only enhances fuel efficiency but also accommodates advanced propulsion systems that may have been challenging to integrate into traditional wing configurations.
The fuselage of the X-66A is a modified McDonnell Douglas MD-90 airframe. Modifications include shortening the fuselage to optimize weight distribution and balance with the new wing configuration. The original wings and engines have been removed to facilitate the installation of the TTBW structure and new propulsion systems.
The X-66A incorporates advanced composite materials in the wing structure, reducing weight while maintaining structural integrity. Traditional aluminum alloys, common in commercial aircraft, have been replaced with high-strength carbon fiber composites, enhancing the aircraft’s strength-to-weight ratio. This material choice contributes to lower fuel consumption and improved overall efficiency.
One of the primary challenges in the TTBW design is flutter suppression. The increased wingspan and reduced thickness make the wings more susceptible to aerodynamic oscillations. To counteract this, Boeing and NASA have implemented active flutter suppression systems, utilizing real-time aerodynamic damping through control surface adjustments.
Another key feature of the X-66A is laminar flow optimization. The ultrathin wings are designed to maintain smooth airflow across the surface, minimizing turbulent separation and drag. Computational fluid dynamics (CFD) simulations and wind tunnel testing have refined this design, ensuring maximum efficiency at transonic speeds.
The landing gear configuration remains largely unchanged from the MD-90, with reinforced structures to accommodate the altered center of gravity and weight distribution. The wing-mounted engines of the original MD-90 have been removed, with new engine placement designed to optimize aerodynamics and reduce noise emissions.
The TTBW configuration offers several advantages:
- Up to 30% fuel savings compared to current single-aisle aircraft.
- Reduced CO₂ and NOₓ emissions, contributing to the aviation sector’s sustainability goals.
- Improved high-altitude aerodynamic performance due to reduced induced drag.
- Potential for hybrid-electric propulsion integration, increasing operational efficiency.
However, there are some drawbacks:
- Structural complexity due to the addition of truss supports.
- Weight distribution challenges, requiring careful balance adjustments.
- Manufacturing and maintenance considerations, as truss-supported wings require different inspection and maintenance protocols.
Despite these challenges, the X-66A’s design represents a crucial step toward developing more fuel-efficient commercial aircraft for the future.
Performance of the NASA-Boeing X-66A TTBW
The X-66A is powered by high-efficiency turbofan engines, designed to maximize fuel efficiency and reduce emissions. While exact engine specifications have not been disclosed, the aircraft is expected to utilize next-generation ultra-high bypass ratio (UHBR) turbofan engines, significantly improving fuel burn compared to conventional engines.
Key Performance Specifications:
- Cruise Speed: Mach 0.80 (~988 km/h or 614 mph), comparable to standard single-aisle jets.
- Range: Estimated at 3,000 nautical miles (5,556 km), suitable for medium-haul operations.
- Maximum Takeoff Weight (MTOW): Estimated at 175,000 lb (79,378 kg).
- Service Ceiling: Expected to exceed 40,000 feet (12,192 meters), consistent with modern commercial aircraft.
The aerodynamic benefits of the TTBW design enhance the aircraft’s range by reducing drag. The longer wingspan allows for greater lift generation at lower speeds, improving takeoff and landing efficiency.
How the X-66A Compares to Competitors:
- Compared to the Boeing 737 MAX: The X-66A’s TTBW configuration offers superior aerodynamic efficiency, resulting in 20-30% lower fuel consumption.
- Compared to the Airbus A320neo: The X-66A’s optimized wing design provides a longer range at similar operating costs.
- Compared to Hybrid-Electric Concepts: The X-66A serves as a transitional technology, demonstrating improvements before the widespread adoption of electric propulsion.
The aircraft’s environmental benefits include reduced NOₓ emissions and lower noise pollution. By integrating sustainable aviation fuels (SAFs) and hybrid-electric propulsion in future iterations, the X-66A could further enhance its operational efficiency.
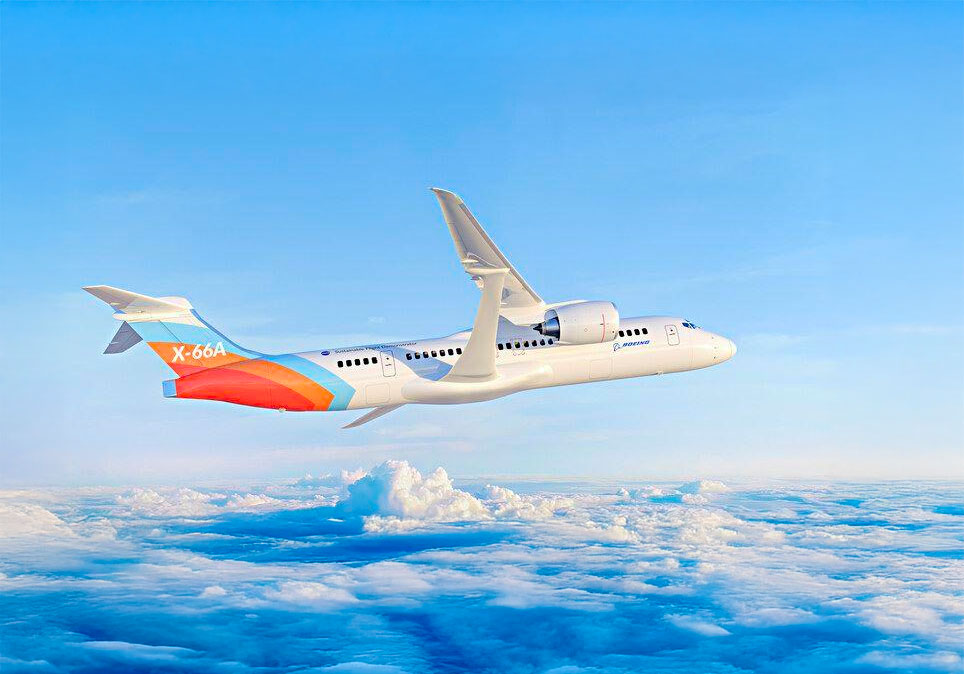
Variants of the NASA-Boeing X-66A TTBW
Currently, the X-66A exists as a single demonstrator variant, but future developments may lead to commercialized adaptations.
- X-66A Baseline: The experimental version based on the MD-90 platform, focusing on aerodynamic efficiency validation.
- Future Production Model: Expected to integrate optimized propulsion systems and lightweight composite structures for commercial deployment.
- Hybrid-Electric Variant: Potential adaptation incorporating hybrid-electric propulsion to further reduce fuel consumption.
Unlike traditional experimental aircraft that remain testbeds, the X-66A’s findings will directly influence future commercial aircraft designs, potentially leading to the next-generation single-aisle aircraft by the mid-2030s.
Military Missions of the NASA-Boeing X-66A TTBW
The X-66A is a civilian research aircraft and is not designed for military applications. However, the Transonic Truss-Braced Wing concept could have military implications.
Potential Military Applications:
- Next-Generation Military Transports: The TTBW design could be adapted for fuel-efficient military cargo planes.
- Aerial Refueling Tankers: Reduced drag could extend loiter times for aerial refueling missions.
- Surveillance and Reconnaissance Aircraft: A high-altitude, long-endurance UAV variant could utilize the aerodynamic advantages of the TTBW configuration.
Competing Military Aircraft:
While the X-66A itself does not compete in military aviation, its efficiency-focused innovations could influence future designs. The closest military analogs include:
- Boeing KC-46 Pegasus (Tanker)
- Lockheed Martin C-130J Super Hercules (Tactical Transport)
- Boeing P-8 Poseidon (Maritime Surveillance)
Despite its civilian focus, the advancements tested on the X-66A could pave the way for future military adaptations.
The NASA-Boeing X-66A is a significant step toward the development of next-generation fuel-efficient aircraft. By demonstrating the feasibility of Transonic Truss-Braced Wing technology, it aims to reduce fuel consumption, minimize emissions, and enhance aerodynamic performance.
Key Takeaways:
- 30% reduction in fuel burn compared to current single-aisle aircraft.
- Mach 0.80 cruise speed with an optimized high-aspect-ratio wing.
- Application of advanced composite materials to reduce weight.
- Potential hybrid-electric propulsion integration for future models.
The X-66A is not intended for commercial production, but its findings will influence the next generation of single-aisle aircraft, expected to enter service by the mid-2030s. The insights gained from this demonstrator will shape the aviation industry’s transition toward sustainable, high-efficiency air travel.
Back to the experimental aircraft section.