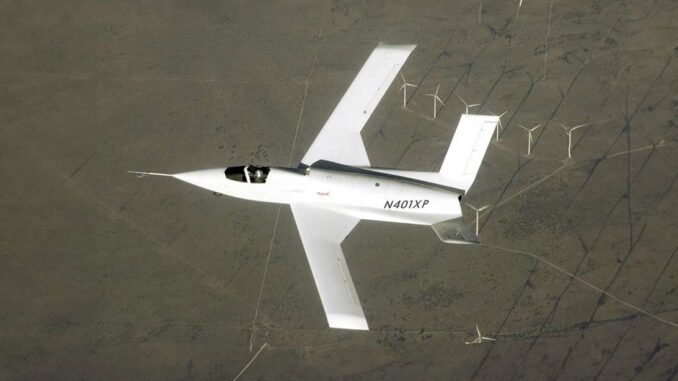
Experimental aircrafts represent the cutting edge of aeronautical innovation. Their development involves a series of rigorous tests to ensure that they are safe, reliable and perform well before being put into service. This technical article explores the different stages and methods used to test experimental aircrafts, from initial design through to flight testing.
Design and Simulation
Before an experimental aircraft is even built, it goes through a detailed design phase that includes numerical simulations and model analysis. Engineers use computer-aided design (CAD) software to create 3D models of the aircraft. These models are then subjected to computational fluid dynamics (CFD) simulations to assess aerodynamic performance. CFD predicts how the air will flow around the aircraft, identifying pressure points, turbulence zones and lift and drag forces.
At the same time, structural simulations are carried out to ensure that the aircraft can withstand the expected loads and stresses. Finite element analysis (FEA) software is used to model the aircraft’s structural behavior under different load conditions. These simulations help optimize the design to minimize weight while maximizing strength.
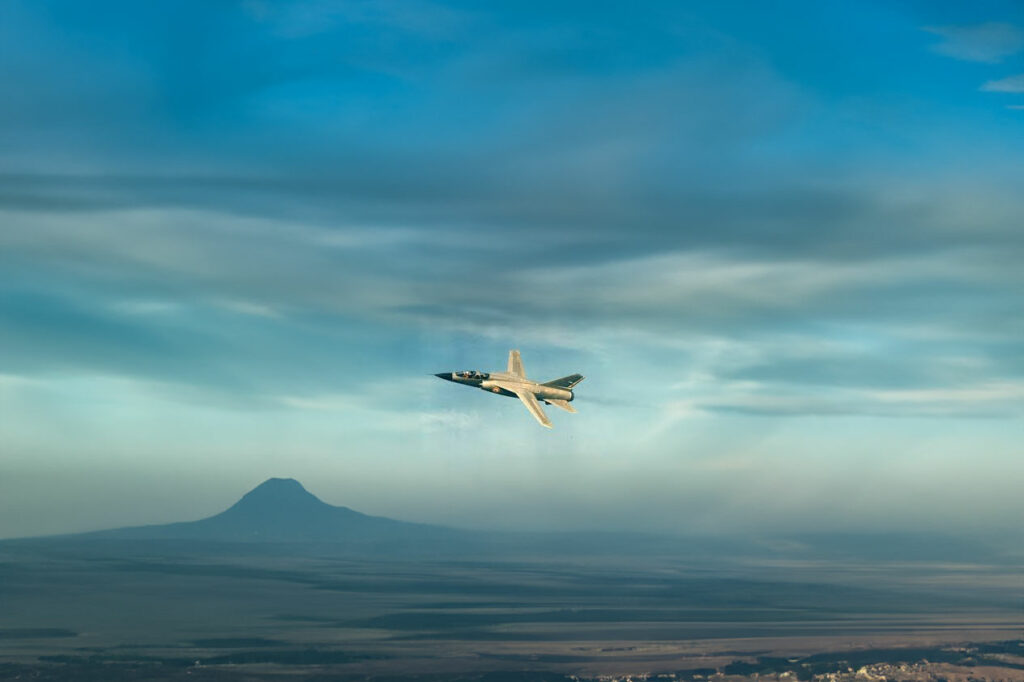
Prototyping and ground tests
Once the numerical models have been validated, one or more physical prototypes are built. The first set of tests takes place on the ground and comprises several crucial stages:
Static testing
Static testing involves applying loads to various parts of the aircraft structure to check its strength and rigidity. These tests can include loads simulating extreme maneuvers, severe turbulence and hard landings. Wings, fuselage, empennage and other critical components are tested to ensure that they can withstand the maximum anticipated loads without permanent deformation or failure.
Fatigue testing
Fatigue tests are designed to assess the aircraft’s durability over a long period. They involve the repeated application of cyclic loads to simulate everyday flight conditions and verify the fatigue resistance of materials and joints. The data obtained from these tests help to predict aircraft life and identify areas potentially prone to cracking or failure.
Systems testing
Systems testing involves checking all on-board systems, including electrical, hydraulic, fuel, flight control and communication systems. Each system is tested individually and in interaction with the others to ensure that they operate correctly and in an integrated manner. Emergency scenarios are also simulated to check system response under critical conditions.
Engine testing
Engine testing is crucial for validating the performance of engines and propulsion systems. These tests include start-up, shutdown, rpm variations and performance tests in extreme conditions. Engines are tested for thrust, fuel consumption, reliability and resistance to heat and vibration.
Wind tunnel testing
Wind tunnel testing is an intermediate step before flight testing. A scaled-down model of the aircraft, or sometimes a full-scale prototype, is placed in a wind tunnel to study aerodynamic characteristics in greater detail. Wind tunnels enable us to precisely control airflow conditions and observe aircraft behavior at different angles of attack and speeds. These tests are essential for fine-tuning the design and solving aerodynamic problems before the first flight.
Flight tests
Once the aircraft has passed ground and wind tunnel tests, it is ready for flight testing. Flight testing takes place in several phases, each designed to verify different aspects of the aircraft’s performance and safety.
Unwinding flights
Rust-out flights are the first flight tests and focus on verifying the aircraft’s basic functions. These flights include simple maneuvers and straight-line flights to check the aircraft’s stability, control and systems response.
Envelope flights
Envelope flights are designed to test the aircraft within its operational limits. These tests include high-speed maneuvers, tight turns, rapid climbs and steep descents to ensure that the aircraft can operate safely in all anticipated conditions. Test pilots carefully monitor the aircraft’s performance and collect data to analyze its behavior.
Performance flights
Performance flights evaluate specific aspects such as fuel consumption, range, maximum speed and rate of climb. These tests are essential to confirm that the aircraft meets the performance specifications defined at the design stage.
Certification flights
Certification flights are carried out in the presence of aviation regulatory authorities to demonstrate that the aircraft meets all safety and performance requirements. These flights include emergency scenarios, forced landings and other critical situations to verify the aircraft’s reliability and safety.
Operational flights
Operational flights simulate real-life mission conditions to verify that the aircraft can perform the tasks for which it was designed. These tests include simulated combat missions for military aircraft, long-distance flights for commercial aircraft and other mission-specific scenarios.
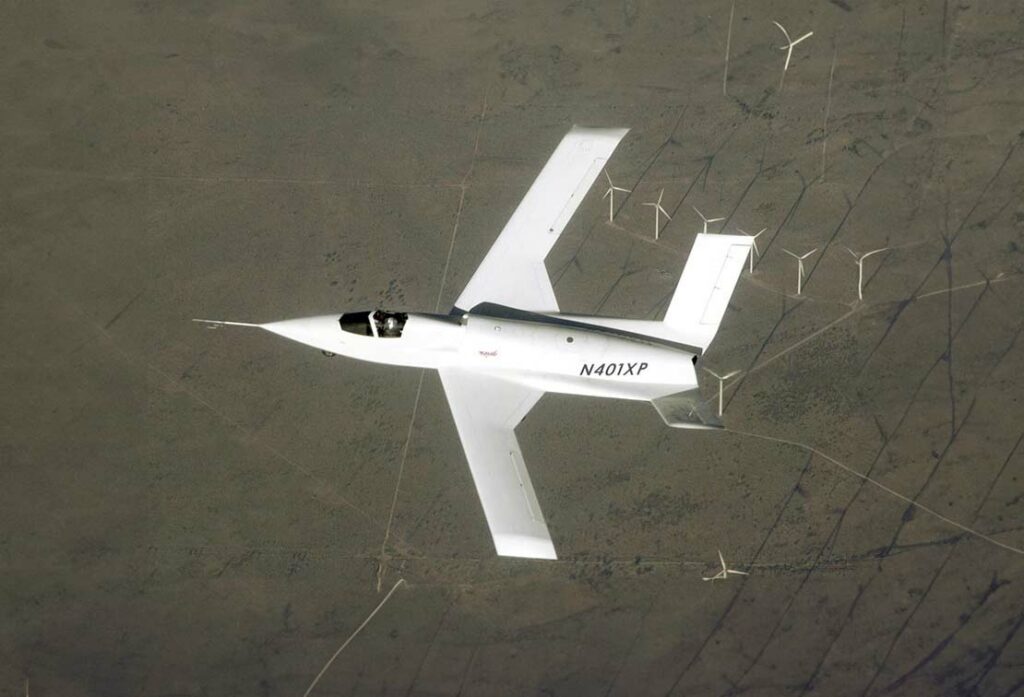
Testing experimental aircraft is a complex and rigorous process involving numerical simulations, ground tests, wind tunnel tests and flight tests. Each step is essential to ensure that the aircraft is safe, reliable and capable of meeting performance requirements. Thanks to these in-depth tests, engineers can identify and solve problems before the aircraft enters service, ensuring the safety and efficiency of new-generation aircraft.
War Wings Daily is an independant magazine.