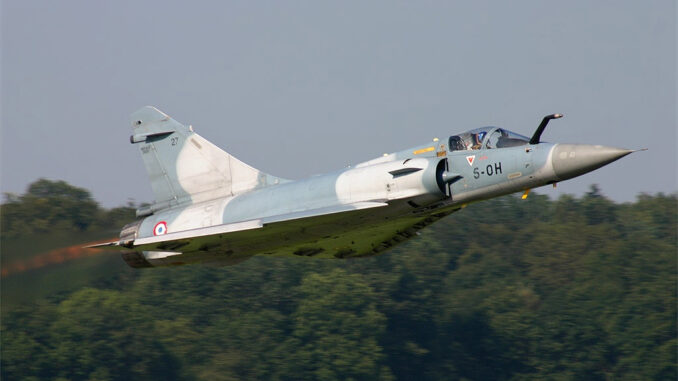
Discover how fighter aircraft propulsion works: engine types, key components, technological innovations and environmental challenges.
Propulsion is essential for fighter aircraft, guaranteeing superior performance in terms of speed, maneuverability and range. These aircraft must be able to reach high speeds, cover long distances and perform complex maneuvers, often in combat situations. Propulsion provides the thrust needed to take off, maintain supersonic speeds and perform demanding aerial maneuvers.
Fighter aircraft use two main types of propulsion: turbojet and turbofan. Each type has specific characteristics tailored to military requirements.
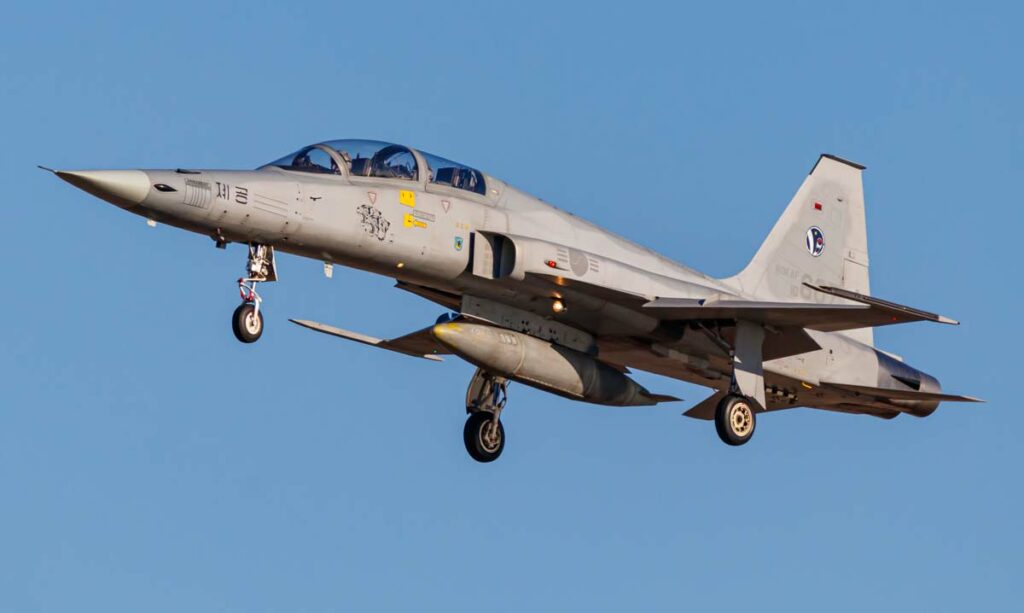
Basic propulsion principles
1. Definition and importance
Propulsion is the process by which an aircraft is pushed forward. In fighter aircraft, propulsion is crucial to achieving the high speeds required for military missions, including rapid maneuvers and interception. Propulsion power and efficiency determine the aircraft’s ability to perform complex maneuvers and maintain supersonic speeds.
Modern fighter jets, such as the Rafale and F-22 Raptor, mainly use jet engines to achieve the necessary performance. For example, the Rafale is equipped with two Snecma M88 engines, each capable of producing 50 kN of thrust dry and 75 kN with afterburner, enabling the aircraft to exceed Mach 1.8.
2. The Brayton cycle
The Brayton cycle is the fundamental principle of the jet engines used in fighter jets. This thermodynamic cycle comprises four stages:
- Compression : Outside air is compressed using a compressor.
- Combustion: Fuel is mixed with compressed air and ignited in the combustion chamber.
- Expansion: Expanding hot gases pass through a turbine, producing mechanical energy to turn the compressor.
- Ejection: The remaining gases are expelled through a nozzle, generating thrust.
This cycle ensures continuous thrust production, essential for maintaining high speeds and maneuverability. For example, the F-22 Raptor’s Pratt & Whitney F119 engine uses this cycle to reach supersonic speeds without afterburning, thus saving fuel and increasing efficiency.
Propulsion is a vital component of fighter aircraft, enabling superior in-flight performance. The Brayton cycle is the key mechanism behind thrust generation in jet engines, ensuring constant, efficient power for complex, demanding operations.
Types of engines used in fighter jets
1. Turbojet engines
Turbojet engines are the most common type used in fighter jets. They operate by compressing air, burning fuel and expelling hot gases to generate thrust. Here are the key stages in this process:
- Air compression : Air is drawn in at the front of the engine and compressed by a compressor.
- Combustion: Fuel, usually kerosene, is injected and mixed with compressed air in the combustion chamber. Combustion of this mixture produces hot gases at high pressure.
- Turbine: The hot gases pass through a turbine, which extracts energy to turn the compressor.
- Ejection: The gases are expelled through the nozzle, generating the thrust needed to propel the aircraft.
Turbojet engines are powerful and capable of operating efficiently at supersonic speeds. However, they consume a lot of fuel and can be noisy.
2. Turbochargers
Turbochargers, also known as turbofans, are an evolution of turbojet engines. They incorporate a large fan at the front of the engine, which compresses the air and directs it around the main engine. This increases efficiency and reduces noise.
- Blower: Much of the air drawn in is directed around the main engine, creating extra thrust with less fuel consumption.
- Airflow: Turbochargers have a high dilution ratio, meaning that a large amount of “cold” air is mixed with the warm air leaving the engine, improving efficiency.
Turbofan engines are most efficient at subsonic speeds, and are often used in commercial aircraft, as well as in some modern fighter jets for operations requiring long range and a low acoustic signature.
3. Afterburning engines
Afterburning engines, or turbofan engines with afterburner, are used to increase thrust considerably, particularly during take-off, rapid climb or aerial combat.
- After initial combustion, additional fuel is injected into the exhaust nozzle, where it is burned. This second combustion significantly increases the temperature and velocity of the expelled gases, generating increased thrust.
- Application : Afterburning enables aircraft like the F-22 Raptor or the Dassault Rafale to reach supersonic speeds and maintain high-performance maneuvers.
However, the use of afterburning drastically increases fuel consumption and produces a significant heat signature, which can make the aircraft more detectable.
These engines, each with their own specific features and advantages, are essential for meeting the varied mission requirements of modern fighter aircraft.
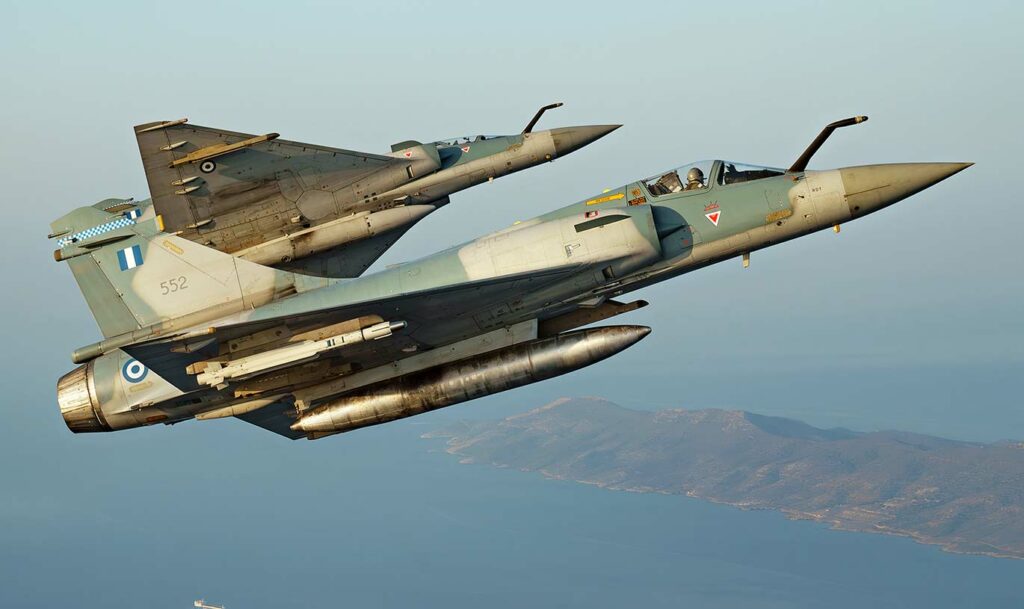
Main components of fighter jet engines
1. compressor
The compressor plays a crucial role in a fighter jet engine. It draws in outside air, compresses it and directs it to the combustion chamber. This increases air density and, consequently, the amount of oxygen available for combustion, thus improving engine efficiency.
Compressor types used:
- Axial compressor: This type of compressor uses a series of rotors and stators. Rotors, with moving blades, increase air pressure by passing it through several stages. The stators, with their fixed blades, straighten the air flow between each stage, increasing the overall pressure at each passage.
- Centrifugal compressor: Less common in modern fighter jets, this type uses a rotor to increase air speed, which is then decelerated in a diffuser, increasing pressure.
Axial compressors are more efficient for fighter aircraft because of their ability to handle high air flows and produce high compression ratios over long distances.
2. Combustion chamber
The combustion chamber is where fuel is mixed with compressed air and ignited. This process produces hot gases at high pressure, which are essential for generating the thrust required by the engine.
Combustion process and thrust generation:
- Air-fuel mixture : Compressed air enters the combustion chamber, where it is mixed with kerosene.
- Combustion : The mixture is ignited, producing high-temperature, high-pressure gases.
- Gas evacuation : The hot gases escape at high speed, passing through the turbine and generating thrust.
Modern combustion chambers, like those used in the M88 engine used in the Rafale, are designed to maximize combustion efficiency while minimizing emissions and fuel consumption.
3. Turbine
The turbine converts the thermal energy of hot gases into mechanical energy. This energy is used to turn the compressor and other engine accessories.
Turbine operation:
- Energy extraction : Hot gases pass through the turbine blades, turning the turbine shaft.
- Energy transmission: This rotation is used to drive the compressor and accessories via transmission shafts.
Turbines for fighter jet engines must be extremely robust to withstand high temperatures (up to 1,500°C) and high rotation speeds (up to 15,000 rpm). They are often made from single-crystal alloys to withstand these extreme conditions.
4. Nozzle
The nozzle is the part of the engine where exhaust gases are accelerated to generate thrust. It plays a crucial role in engine efficiency and performance.
Role of the nozzle in gas ejection: Gas acceleration
- Gas acceleration : The nozzle converts the thermal energy of the gases into kinetic energy, increasing their ejection speed.
- Thrust control : Nozzles can be designed to vary their outlet cross-section, enabling thrust to be optimized according to flight conditions.
Variable geometry nozzles, like those used on the Rafale, enable thrust to be adjusted more effectively, improving overall aircraft performance, particularly during take-off and combat.
Innovations and advanced technologies
1. materials and design
Use of modern materials to enhance performance and durability
Recent innovations in materials have transformed fighter aircraft design. Carbon fiber composites, for example, are widely used for their lightness, strength and durability. These materials make it possible to build faster, more fuel-efficient aircraft. Composites are also resistant to fatigue and corrosion, extending the life of aircraft components.
Advanced materials such as titanium alloys and ceramic matrix composites are used for parts that have to withstand extremely high temperatures, such as engine turbines. Ceramic matrix composites offer low density, high hardness, and thermal and chemical resistance, making them ideal for high-temperature applications.
Advances in aerodynamic design Aerodynamic design plays a key role in the design of engine components.
Aerodynamic design plays a crucial role in enhancing fighter aircraft performance. Optimized shapes reduce drag and improve maneuverability at high speeds. For example, the F-22 Raptor uses advanced design techniques to minimize its radar signature and improve stealth. In addition, the integration of composite materials in the aircraft’s structure reduces weight while maintaining high robustness.
2. Digital control systems
The introduction of digital control systems in engines.
Digital control systems, such as FADEC (Full Authority Digital Engine Control), are becoming increasingly common in fighter jet engines. These systems enable precise, automatic management of engine parameters, optimizing performance and fuel consumption. FADEC controls all aspects of engine operation, from compression ratio to gas temperature, ensuring optimum performance in all circumstances.
Performance and safety benefits
The use of digital control systems offers several advantages. They improve the responsiveness and precision of flight controls, which is crucial for complex, high-speed maneuvers. For example, the Mitsubishi X-2 uses optical flight controls (fly-by-optics), offering faster and more precise response than traditional systems, thus improving the aircraft’s maneuverability.
In terms of safety, digital systems enable real-time monitoring of the status of the engine and other critical systems, detecting anomalies before they become serious problems. This reduces the risk of in-flight breakdowns and enables predictive maintenance, optimizing maintenance intervals and reducing long-term operating costs.
These technological innovations and advances in hardware and software are essential to maintaining the competitiveness and efficiency of modern fighter aircraft. They not only improve aircraft performance and durability, but also ensure safer, more efficient operations.

Environmental impact and future challenges
1. emissions reduction
Efforts to reduce emissions of CO2 and other pollutants
The aviation industry is striving to reduce its emissions of CO2 and other pollutants through various initiatives and technologies. The International Civil Aviation Organization (ICAO) has introduced strict CO2 emission standards applicable to all new aircraft models from 2020. These standards aim to integrate the latest emissions-reducing technologies into new aircraft designs, ensuring a continued reduction in the environmental impact of aviation.
Sustainable aviation fuels (SAF) represent another significant advance. They reduce CO2 emissions by an average of 80% over the fuel’s life cycle. Air France, for example, plans to incorporate 10% SAF into its flights by 2030, with an ambition of 63% by 2050.
Current and future technologies for greener engines
Research into hybrid and electric engines is ongoing to offer greener solutions. Airbus is working on hybrid electric propulsion projects and aims to introduce a hydrogen-powered commercial aircraft by 2035. These technologies promise to significantly reduce emissions of CO2 and other pollutants by replacing fossil fuels with cleaner energy sources.
2. Fuel consumption
Optimizing fuel consumption
Optimizing fuel consumption is essential to reducing the carbon footprint of aircraft. New-generation aircraft, such as the Airbus A350 and Boeing 787, use lightweight composite materials and more efficient engines, enabling a 25% reduction in fuel consumption compared with previous models. Air France is investing heavily in fleet renewal, which should reduce CO2 emissions by 30% per passenger kilometer by 2030.
Energy efficiency challenges
Despite these advances, improving the energy efficiency of aircraft engines remains a complex challenge. Designing engines capable of operating efficiently at extreme temperatures and pressures requires advanced materials and technologies. The use of ceramic matrix composites and titanium alloys is helping to meet these requirements, but challenges remain in terms of durability and cost.
The aerospace industry is committed to reducing its environmental impact by adopting innovative technologies and optimizing energy efficiency. However, achieving ambitious targets such as carbon neutrality by 2050 will require ongoing research and development efforts.
War Wings Daily is an independant magazine.