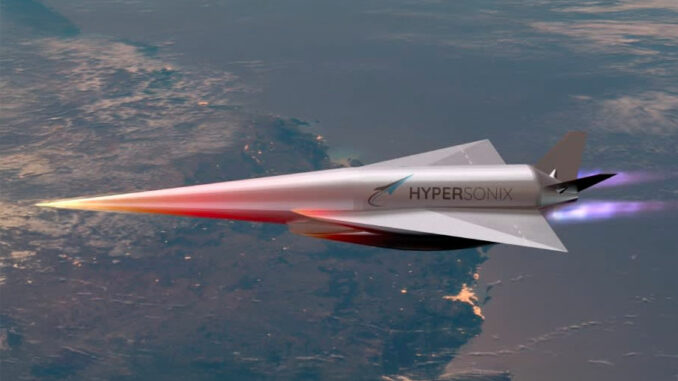
Discover hypersonic engine technologies, how they work, their current performance and future prospects for aeronautics.
Hypersonic engines represent a major advance in aeronautical propulsion, enabling vehicles to exceed speeds of Mach 5, or more than 6,125 km/h. Aimed at an audience of aeronautical engineers, this article offers a detailed analysis of the technologies that power these engines, focusing on their operation, performance, efficiency and future prospects.

How hypersonic engines work
Hypersonic engines operate on the same principle as ramjet propulsion, but at speeds where the air flows even faster. The most studied engine in this field is the scramjet. Unlike conventional jet engines, it has no moving parts to compress the incoming air. Air compression relies entirely on the high speed of the engine, making for a simpler, lighter design.
Scramjet operating principle
In a scramjet engine, incoming air is slowed but remains at supersonic speeds as it passes through the combustion chamber. It is then mixed with a fuel – usually hydrogen – which is injected and ignited. At these speeds, combustion must be stabilized to prevent the fuel from being ejected before it has burned completely.
This process involves several key steps:
- Aerodynamic compression: Air enters the engine’s air intake and is compressed solely by the speed of the engine.
- Injection and supersonic combustion: Hydrogen is injected into the compressed air, then ignited. Unlike conventional jet engines, the air in the combustion chamber remains supersonic.
- Expansion and thrust: The burnt gases escape at high speed through the nozzle, generating hypersonic thrust.
Operating range and thermal constraints
Scramjets are optimized for speeds between Mach 5 and Mach 15 (around 6,125 km/h to 18,375 km/h). By comparison, a conventional turbojet engine becomes ineffective above Mach 3, as its compressors can no longer cope with high speeds.
However, hypersonic flight generates extreme temperatures in excess of 2,000°C on exposed surfaces. To prevent component deterioration, advanced materials such as ultra-refractory ceramics and ceramic matrix composites are used to protect the combustion chamber and engine structure.
Application example
A concrete example of a scramjet engine is NASA’s X-43A, which reached Mach 9.6 in a flight test in 2004. This test confirmed that supersonic combustion was viable and that the scramjet could operate stably at extremely high speeds.
Research is continuing to improve the reliability of scramjets, notably by optimizing fuel injection and thermal management, with a view to developing military and civil applications for hypersonic flight.
Hypersonic engine performance
Hypersonic engines are designed to operate at extreme speeds, where aerodynamic and thermal conditions are totally different from conventional subsonic and supersonic engines. Their range of efficiency lies between Mach 5 and Mach 15 (around 6,125 km/h to 18,375 km/h). At these speeds, airflow dynamics and thermal management are major challenges for maintaining engine stability and efficiency.
Speed and energy efficiency
Supersonic combustion ramjets (scramjets) require no compressor or turbine, which reduces their mass and complexity. However, their energy efficiency remains lower than that of conventional jet engines at low altitudes and speeds. They become more efficient at very high altitudes (between 30 and 50 km) where air density is low, thus minimizing drag.
One of the most striking tests was carried out in 2004 with NASA’s X-43A, which reached Mach 9.6 at an altitude of around 33 km. More recently, China tested an engine capable of reaching Mach 16, or around 19,600 km/h.
Thermal constraints and advanced materials
Temperatures in hypersonic flight exceed 2,000°C due to air compression and friction. This calls for the use of high-temperature-resistant materials, such as :
- Ceramic matrix composites (CMC): used for the combustion chamber and nozzle.
- Refractory alloys (niobium, hafnium, tungsten): for thermal linings.
- Active cooling materials: to dissipate heat through the circulation of a heat-transfer fluid.
Optimizing performance with detonation motors
A recent innovation is rotary detonation engines, which use supersonic detonation waves to improve energy efficiency. Unlike conventional scramjets, they enable faster, more efficient combustion, reducing fuel consumption and increasing thrust. This principle could improve the overall performance of hypersonic engines, making them viable for both military and civil applications.
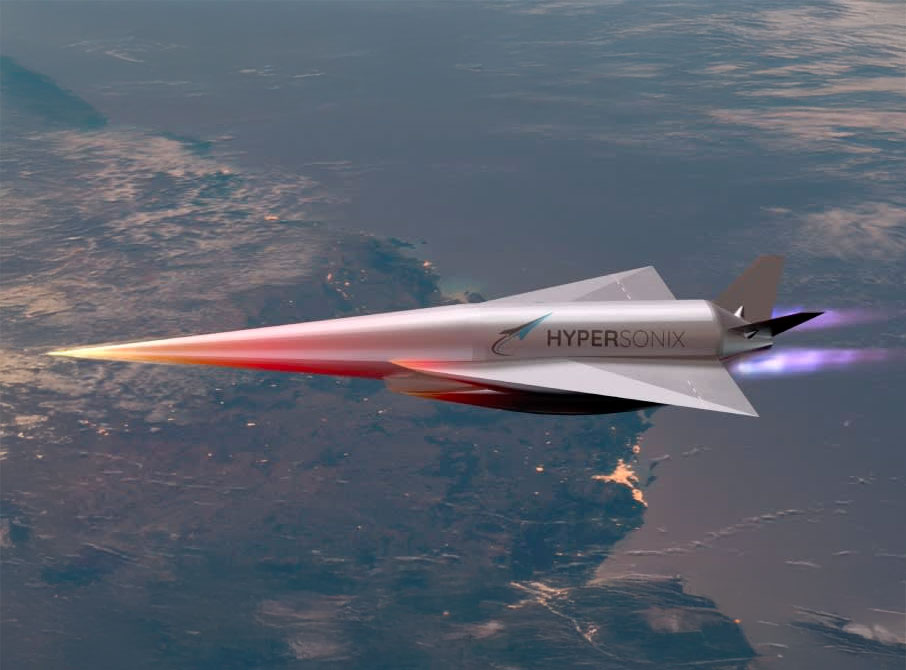
Future prospects for hypersonic engines
Hypersonic engines are an active field of research, with innovations aimed at increasing their performance, reliability and energy efficiency. Current developments focus on improving supersonic combustion, reducing thermal drag and optimizing high-temperature materials.
Aerodynamic morphing engines
One of the major breakthroughs concerns aerodynamic morphing engines. These engines use adaptive structures capable of modifying their geometry according to speed and flight conditions. The aim is to optimize airflow and combustion efficiency while reducing thermal resistance. This technology could lead to better airflow control and more stable thrust at different altitudes and speeds.
Integration of detonation engines
Rotary and oblique detonation engines are also the subject of extensive research. Unlike conventional scramjets, these engines exploit detonation waves to generate more efficient thrust. They could increase combustion power, improve the range of hypersonic craft and enable speeds in excess of Mach 15. In 2022, China tested an engine incorporating these principles and capable of reaching Mach 16 (19,600 km/h).
Potential applications
Hypersonic engines are being considered for both military and civilian applications:
- Hypersonic missiles: development of systems capable of maneuvering at high speed, evading defense systems.
- Rapid air transport: possibility of linking two continents in less than 2 hours.
- Access to space: integration into reusable space vehicles to reduce orbiting costs.
These innovations still require testing and validation, but they could radically transform aeronautics and astronautics over the coming decades.
Hypersonic engines, including scramjets and rotary detonation engines, represent the future of very high-speed aeronautical propulsion. Although technical challenges remain, recent advances are paving the way for potential applications in both the military and civilian fields, with considerably reduced travel times and new opportunities for space exploration.
War Wings Daily is an independant magazine.