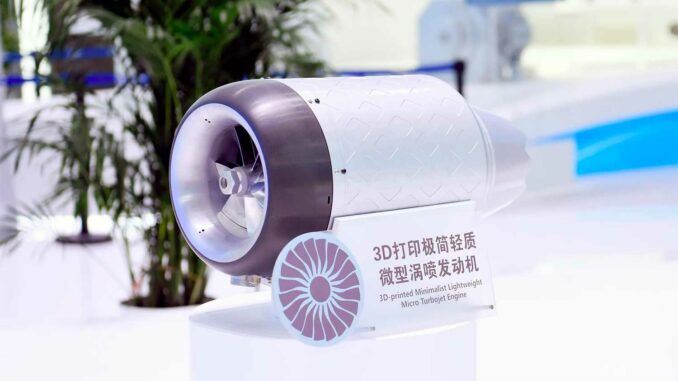
A 3D-printed turbojet engine with 160 kg of thrust flew at an altitude of 4,000 meters, validating its stability for drones and light missiles.
China has successfully flown a 3D-printed turbojet engine with 160 kilograms of thrust, designed by AECC (Aero Engine Corporation of China). The engine reached 4,000 meters in altitude during its test in Inner Mongolia. This is the first Chinese turbojet engine of its kind to be manufactured entirely using optimized design and additive manufacturing. The objective is twofold: to reduce weight while maintaining high thermal and mechanical performance. This breakthrough is aimed at future reconnaissance drones, cruise missiles and autonomous light strike platforms. The use of 3D printing reduces development times, simplifies the industrial chain and eliminates the need for critical suppliers. This test places China among the few countries capable of producing a complete, tested and operational printed engine.
Successful flight validates reliability in real-world conditions
The turbojet engine was flight tested over Inner Mongolia. The engine operated at an altitude of 4,000 meters, demonstrating its thermal stability, structural strength, and ability to withstand atmospheric pressure variations. This altitude corresponds to the typical operating environment of many short- and medium-range military drones. The 160-kilogram thrust allows the engine to be used in tactical drones or light missiles without the need for secondary propulsion stages.
In comparison, small turbojet engines used on Western cruise missiles or conventional MALE drones produce between 150 and 300 kilograms of thrust for masses ranging from 50 to 70 kilograms. The engine tested by AECC therefore has a competitive thrust-to-weight ratio, which is a key performance indicator for airborne vehicles.
This achievement marks a first in China: no other engine with equivalent thrust had been developed in-house using full additive manufacturing, nor had it been tested in flight. This allows Beijing to strengthen its technological base in critical components for light aircraft engines.
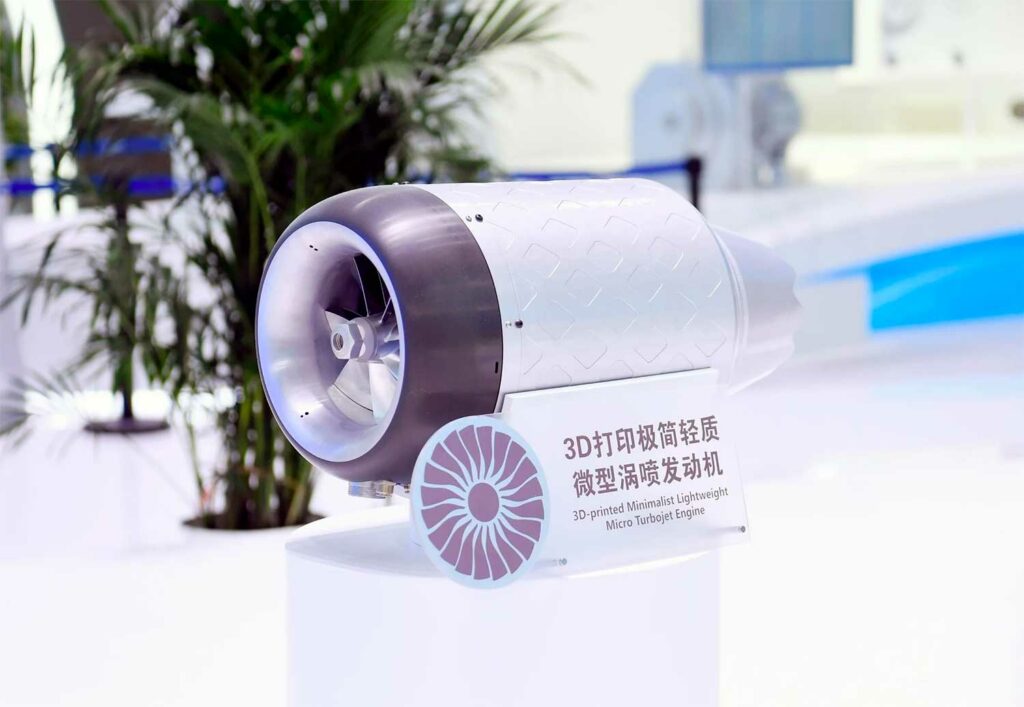
A design optimized by multi-disciplinary topology
The engine was designed using a multi-disciplinary topology method, which means that engineers simulated thermal, mechanical, and aerodynamic stresses before printing each part. This approach reduces the total weight of the engine by 20 to 30% while maintaining structural safety margins.
The materials used, such as titanium alloys and nickel-based superalloys, are printed layer by layer using laser fusion, ensuring resistance to temperatures above 1,000°C. The process eliminates the need for traditional assembly techniques (welding, riveting, brazing), which limits areas of mechanical weakness and reduces manufacturing lead times.
Full additive manufacturing also reduces prototyping times to a few weeks, compared to several months in conventional manufacturing. This speed gives AECC a strategic advantage in accelerating the development of variants or new models. From an industrial standpoint, the engine is a textbook case: it demonstrates that the production chain can be simplified without compromising reliability or performance standards.
Immediate applications for tactical drones and missiles
This type of compact engine is intended for several aerial platforms currently under development in China. In the field of drones, it is suitable for tactical reconnaissance aircraft or light attack drones. A 2-ton drone equipped with an engine of this class could fly at a speed of 600 km/h, with a 15 to 20% increase in range compared to a heavier conventional engine.
For missiles, this engine would enable the design of 1,000 to 1,500 kilometer range vehicles flying at constant subsonic speed, while remaining compact and discreet. The engine could also be used to equip new-generation loitering munitions or reusable platforms.
According to market trends, tactical drones and smart missiles represent a rapidly growing segment: the global market for lightweight drone engines is estimated at more than $2.5 billion by 2025, with an annual growth rate of close to 12%. By validating a lightweight 3D-printed motor, China is positioning itself to equip its own forces and offer solutions for export, particularly to allies and partners in Asia, Africa, and the Middle East.
Concrete industrial and strategic implications
The engine developed by AECC enables China to reduce its technological dependence on Western suppliers. Until now, critical propulsion components for drones and missiles were often purchased from foreign partners or copied from older technologies. The complete integration of a lightweight 3D-printed engine enables rapid, responsive local production that is difficult to ban through sanctions.
Economically, 3D printing can reduce production costs by 25 to 30% according to available estimates, particularly by limiting the need for tooling, assembly lines, and complex logistics. This provides additional flexibility to design, test, modify, and produce variants tailored to specific mission profiles.
Finally, from a strategic standpoint, 3D printing of complete engines makes supply chains more resilient. In the event of conflict or trade restrictions, additive manufacturing makes it possible to maintain local war production, even in constrained environments.
Technological limitations and remaining critical steps
Despite this in-flight success, several technical challenges still need to be overcome before large-scale industrial production can begin. First, the reproducibility of printed parts remains a major issue. Non-destructive testing systems (ultrasound, radiography, tomography) need to be integrated to ensure that there are no internal defects.
Next, service durability will have to be demonstrated through test cycles under extreme conditions: prolonged vibrations, intense thermal cycles, and salty or sandy atmospheres. This is a prerequisite for certification for military use and, even more so, for civilian use.
Finally, the industry will have to adapt its standards to the specificities of 3D printing. Organizations such as the CAAC, EASA, and FAA will have to validate standards to regulate the design, traceability, and maintenance of this type of engine.
The success of the maiden flight therefore marks an undeniable technical breakthrough. But its transition to a reliable, large-scale operational solution will depend on China’s ability to transform this demonstration into a qualified, stable, and certified production line.
War Wings Daily is an independant magazine.