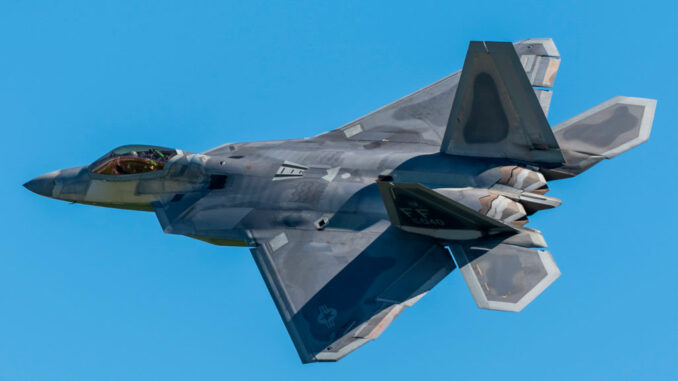
Composite materials have revolutionized the design of fighter planes. Technical detail and feedback on their industrial and military influence.
Composite materials have changed the design of fighter planes since the 1970s. Their use is not the result of a fashion trend but of a technical necessity. Aerodynamic constraints, maintenance costs, stealth requirements and pressure on operational performance have pushed the industry to abandon some of the metal. Aluminum alloy, once central to military aeronautics, no longer meets the needs of modern combat aircraft. Carbon fiber reinforced polymers, ceramic or thermoplastic matrix composites are now present in airframes, wings, air intakes and control surfaces. The sector has not adapted by choice, but by industrial necessity. The initial costs are high, but the operational and tactical gains make up for this. This evolution in materials has a direct impact on the doctrine of use and the military aeronautical production chains.

Composite materials in the structure of fighter planes
The rise of composite materials can be explained first and foremost by their density. Carbon-epoxy has an average density of 1.6 g/cm³, compared with 2.7 g/cm³ for aluminum and 4.5 g/cm³ for titanium. The weight saving can sometimes reach 20 to 25% on certain airframes. This differential directly improves the thrust-to-weight ratio and the payload capacity.
The Lockheed Martin F-22 Raptor incorporates around 24% composites in its airframe, particularly for the control surfaces, leading edges and fin. The Dassault Rafale has 70% composite materials on its exposed surfaces, with a weight gain of 500 kg compared to an all-metal structure. This makes it possible to compensate for the weight of the modular electronic systems and weapons without sacrificing autonomy.
The production of composites requires heavy industrial processes: high-pressure autoclaves, laser cutting, structural bonding, and non-destructive ultrasonic testing. A composite cell requires more machining time but reduces the need for riveting and welding. The F-35 Lightning II is a good example of this: despite long assembly times, maintenance is simplified by replaceable one-piece panels.
The cost per kilogram of woven carbon fiber ranges from €40 to €70, depending on the quality and weave. The production cost is higher than aluminum, but the life cycle is longer and inspections are less frequent. The armed forces accept this additional cost because it reduces operational downtime.
Additive manufacturing in composite materials is also progressing. Secondary parts or internal ducts can be manufactured by fused deposition modeling (FDM) or laser sintering with carbon or Kevlar fillers. These processes reduce maintenance times on advanced bases.
The impact of composites on stealth and operational performance
Fifth-generation fighter planes can no longer do without composite materials, not only for weight, but also for radar signatures. Composite surfaces incorporate radar-absorbent materials (RAM). These coatings make it possible to lower the radar cross-section (RCS) by several orders of magnitude.
The F-35 has an ERS of less than 0.005 m², compared with 1 to 3 m² for a conventional fourth-generation metal fighter. This reduction is largely made possible by the use of absorbent materials integrated into the coating composites, avoiding right angles and multiplying absorbent curved shapes.
The Sukhoi Su-57, although more modest in its use of composites (about 25% of the airframe), also incorporates absorbent polymers in its air intakes and tail fins. China, with the Chengdu J-20, is pushing further the integration of RAM into a composite structure estimated at 40%.
These choices have direct operational consequences. An aircraft with a reduced SER can engage or reposition itself without being detected. This changes the doctrines of deep penetration, electronic support and air superiority.
However, the technical constraint remains strong. RAM surfaces are sensitive to abrasion and moisture and require specific repairs. Each impact on a composite structure may require the complete removal of the panel for inspection, unlike metal sheets that can be repaired locally.
Finally, composites alter the thermal regimes of aircraft. The coefficient of thermal expansion is very low, but heat transfer is lower than in metal. This requires independent thermal management systems for electronic bays and internal armaments.
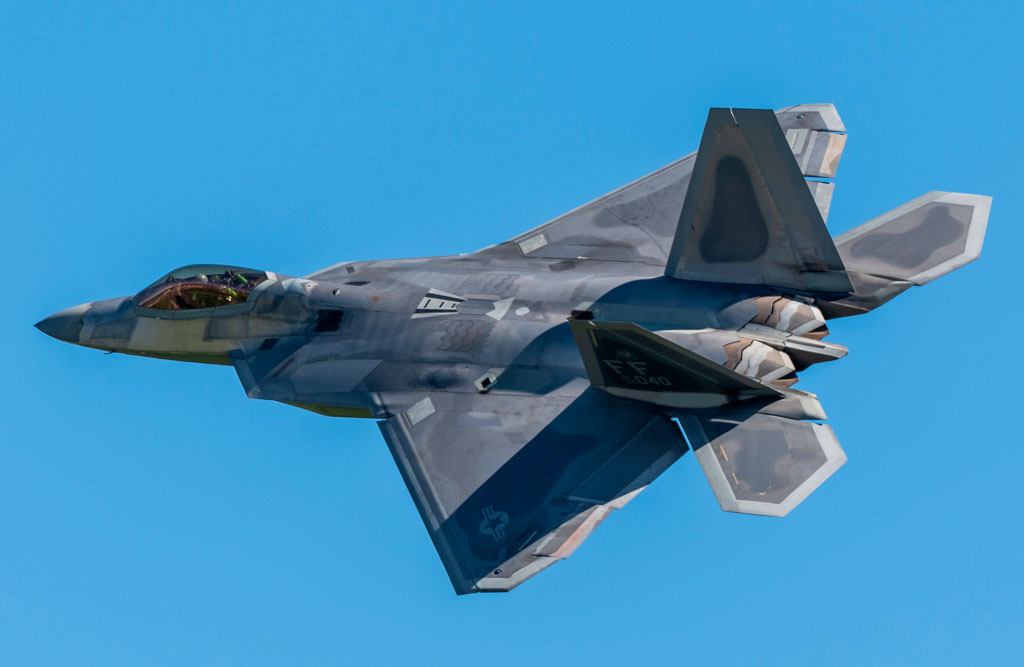
The influence on the industrial chain and the doctrine of use of fighters
The introduction of composite materials is disrupting the entire aeronautical industrial chain. Traditional production centers, equipped for aluminum milling, are outdated. Composite manufacturing relies on robotic fiber placement, automated draping, and long curing cycles, with an average cycle time of 6 to 12 hours per part.
The F-35 required the construction of a specific automated draping line in Lockheed Martin’s factories. At Dassault, the Rafale required the restructuring of the Mérignac line to integrate bonding and curing processes. The initial investment for a complete composite line often exceeds €300 to €500 million.
Logistics are also changing. Parts can no longer be stored like metal components. Storage requires air-conditioned environments, especially for uncured resins.
From an operational point of view, this means a reduction in field repair teams, but an increase in specialized technicians. Maintenance is becoming more specialized, less improvised. Some armies struggle to maintain this level of technicality in expeditionary contexts.
The use of composite materials also requires new NATO certification standards. Ballistic impact resistance, heating in supersonic flight or catapulting stresses (for carrier aircraft) must be recalculated according to fatigue matrices other than those for aluminum.
The use of composites, however, makes it possible to standardize certain parts across several platforms. The Rafale, the nEUROn and the Falcon 10X share certain draping, bonding and assembly technologies. This pooling reduces costs and facilitates cross-development between civil and military aviation.
War Wings Daily is an independant magazine.