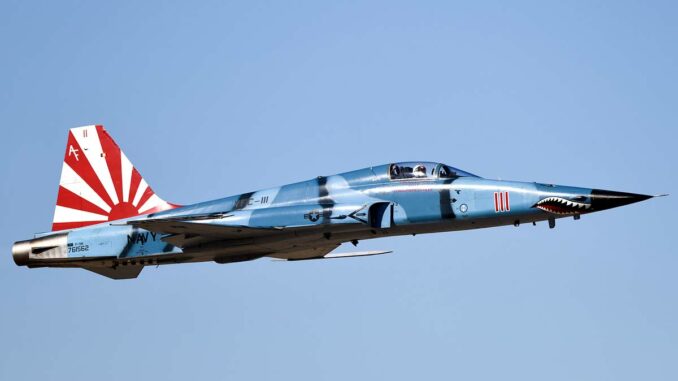
Discover the essential tests carried out on fighter aircraft prior to certification to guarantee safety and performance.
In the world of fighter aircraft, pre-certification testing is of paramount importance to ensure safety and performance. Before a fighter aircraft is certified for flight, it must pass a series of rigorous tests. These assessments are designed to ensure that each aircraft meets the stringent safety and operating standards demanded by aviation regulators such as the European Union Aviation Safety Agency (EASA) and the US Federal Aviation Administration (FAA). The rigor of these tests reflects our commitment to the flight safety and operational reliability of combat aircraft.
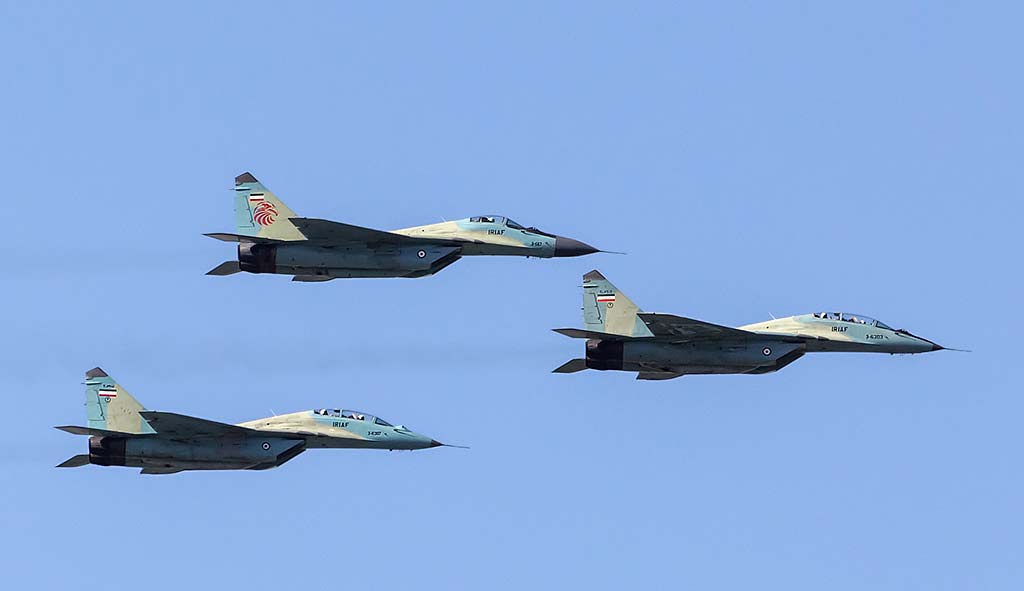
Understanding certification standards
Explanation of certification criteria for fighter aircraft
Fighter aircraft, like all other types of aircraft, must obtain a type certificate before entering service, attesting that they meet the safety standards set by regulatory authorities. Certification criteria include design tests, performance evaluations and flight tests to guarantee the safety and reliability of the aircraft.
Certification tests may include structural strength tests, electronic and mechanical system evaluations, endurance tests, and simulations of different flight scenarios to ensure that the aircraft can operate safely under all expected conditions. For example, Airbus conducted a flight test campaign for the A350 that lasted over 14 months and involved more than 2,600 flight hours.
Certification bodies and their role
Major aviation certification bodies include the Federal Aviation Administration (FAA) in the USA and the European Union Aviation Safety Agency (EASA) in Europe. These bodies are responsible for ensuring that aircraft meet rigorous safety and performance standards before they enter service.
- FAA : The FAA uses a certification process that includes review of proposed designs, ground and flight testing, and assessment of the aircraft’s maintenance requirements and operational suitability for service. It also works with other civil authorities to approve aircraft for import into the USA.
- EASA**: EASA, which covers all European Union member states and certain non-member countries, is known for its rigorous requirements, particularly in terms of environmental protection and noise reduction. EASA standards are often considered more prescriptive, involving regular checks and maintenance audits.
Each organization has its own approach to certification, but both aim to ensure that aircraft operate to the highest safety standards to protect passengers and crew.
Design and development testing
Wind tunnel testing: assessing aerodynamic performance
Wind tunnel testing is essential for assessing the aerodynamic performance of fighter aircraft. These tests enable us to visualize and measure changes in airflow around aircraft models at different speeds and altitudes. For example, engineers use wind tunnels to test model aircraft, which can be subjected to speeds up to more than twice the speed of sound. These tests are crucial for refining aircraft design, in particular for optimizing stability and control, as well as integrating engine and air intake performance.
In facilities such as those at ARA in the UK, tests are carried out in low-speed tunnels for speeds down to Mach 0.27, and in high-speed tunnels covering a range from Mach 0.4 to 3.7. These tunnels are used to test elements such as the separation of a fighter aircraft’s magazines, a crucial step in guaranteeing the safety of the aircraft and pilots when dropping ammunition.
Numerical simulations: verification of design and strength of materials
Numerical simulations, in particular the use of computational fluid dynamics (CFD), play a complementary role to wind tunnel testing. They enable aerodynamic performance to be simulated and analyzed before and after wind tunnel testing. These simulations help predict the pressure distribution around the aircraft and the forces acting on it, which is crucial for the design of high-performance aeronautical structures and systems. CFD simulations are particularly useful for testing complex configurations and validating the performance of physical models tested in wind tunnels.
These two methods, wind tunnel testing and numerical simulations, are integrated to develop aircraft that meet the highest standards of performance and safety, enabling engineers to test configurations and innovations without the constraints of real flight testing. This hybrid approach maximizes the efficiency of aircraft development and reduces the costs and risks associated with testing new aircraft concepts.
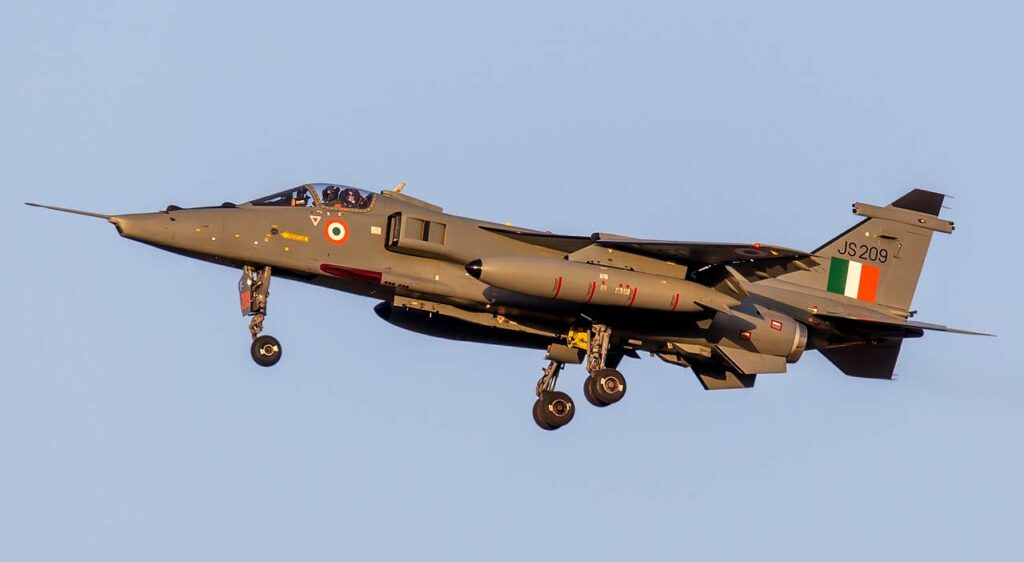
System and component testing
Electronic and navigation systems testing
Electronic and navigation systems on military aircraft undergo rigorous testing to ensure their reliability and accuracy under real-life conditions. These systems include GPS, inertial navigation and communication systems. For example, Honeywell has developed alternative navigation technologies to ensure continuous navigation even when GPS signals are unavailable or disrupted. Similarly, GE Aerospace has implemented Flight Management Systems (FMS) that automate a variety of in-flight tasks, helping to reduce pilot workload and improve operational efficiency through flight path optimization.
Weapons and safety systems assessment
Weapon and security systems are essential to military mission performance, and their evaluation includes tests of resilience against electronic threats. For example, the Defence Research Establishment of Canada (DRDC) conducted tests on the new M-code GPS signal, designed specifically for military applications. This signal improves defense against jamming, spoofing and unauthorized access, guaranteeing uninterrupted GPS navigation for the armed forces.
In addition to these electronic systems, tests are also carried out on the physical and software components of weapons systems to ensure their proper functioning. Air force avionics, for example, undergo regular inspection and maintenance to ensure that all electronic equipment, including radar and weapon control systems, are in perfect working order.
These tests and evaluations are crucial not only to operational safety but also to mission effectiveness, ensuring that all systems function optimally in a variety of operational scenarios.
Flight tests
Flight test phases: from first flight to performance testing under extreme conditions
Flight testing of military aircraft is structured into several essential phases to guarantee safety, performance and compliance with military specifications. These phases generally begin with ground verification tests, followed by a first flight, which focuses on the aircraft’s basic systems. Testing then progresses to performance evaluation flights, where the aircraft is pushed to the limits of its operational capabilities. These include tests of structural strength, maneuverability, endurance, and other critical aspects under various weather and load conditions.
During these phases, every system on the aircraft, including navigation, communications and weapons systems, is thoroughly tested. Tests in extreme situations, such as high- and low-altitude flight, supersonic speeds and complex maneuvers, are also carried out to assess the aircraft’s robustness under simulated combat conditions.
Specific scenarios for combat aircraft: maneuvers, resistance and efficiency in simulated combat
Combat aircraft undergo specific scenario tests that simulate real-life combat conditions. These tests include air combat maneuvers, attack and defense simulations, and weapons system effectiveness tests. The aim is to ensure that the aircraft can not only survive in combat, but also carry out its missions effectively.
Exercises such as circling combat, simulated ground attacks and missile evasion tests are commonplace. These scenarios test the responsiveness of the aircraft’s systems to a variety of threats, and assess the pilots’ ability to operate the aircraft under conditions of high stress. These tests are crucial in determining the aircraft’s ability to accomplish its missions in hostile environments and against a variety of enemy strategies.
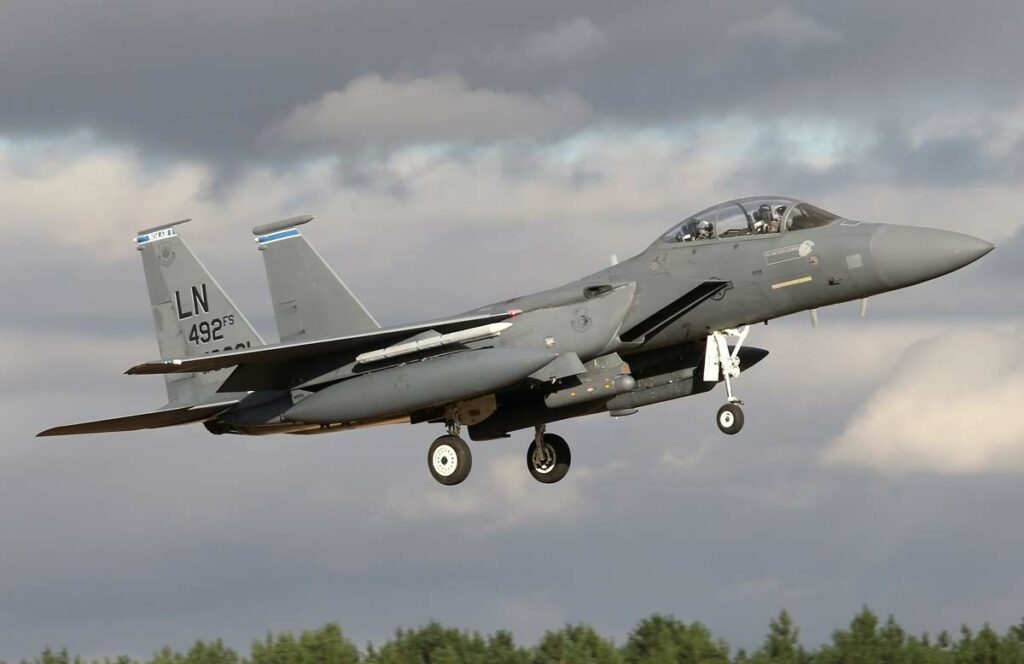
Pre-certification inspection and maintenance
Detailed inspection procedures to ensure compliance with standards
Before certification, military aircraft undergo detailed inspections to ensure they meet all required safety and performance standards. These inspections include examination of the aircraft’s structure, propulsion systems, electronic and navigation systems, and safety equipment. According to the AS/EN 9100 standard, which is specific to the aerospace sector, inspections aim to establish an effective quality management system to maintain and improve the safety and reliability of aerospace products.
Preventive maintenance and correction of anomalies discovered during testing
Preventive maintenance is essential to prevent potential failures before they occur. It includes regular checks on critical components, replacement of worn parts and updating of software systems. If anomalies are discovered during testing, corrective measures are taken to resolve these problems before the aircraft is finally certified. These measures may include repairs or replacement of components, as well as adjustments to operating procedures.
The European Union Aviation Safety Agency (EASA) has established strict guidelines for maintenance certification, requiring detailed records of all interventions and repairs carried out. These records ensure that any anomalies are dealt with in accordance with established standards, and enable accurate assessment during subsequent audits.
Perspectives on the future evolution of test procedures with technological advances
The evolution of test procedures for military aircraft is being transformed by technological advances, particularly with the integration of modular architectures and open systems. These innovations promise to increase the flexibility, safety and efficiency of aircraft testing, while reducing costs and lead times.
- Adoption of modular systems: Open and modular systems are becoming essential for future military aircraft. These systems enable faster integration of new technologies, and facilitate upgrades without the need for complete platform overhauls. Moving to open architectures enables military planners to reduce platform lifecycle costs while increasing operational agility. Initiatives such as the US Army’s Future Vertical Lift illustrate this transition to an Open Modular Systems (MOSA) approach, which facilitates the adoption of new innovations while maintaining the performance of existing technologies.
- Flying laboratories for technological maturity: Flight test platforms, such as the Airbus Flightlab, play a crucial role in the maturation of future technologies. These flying laboratories enable innovations that cannot be fully validated by advanced modeling alone to be tested under real-life conditions. These include the integration of new avionics technologies, improved propulsion systems and advanced sensors. The Airbus Flightlab, for example, tests technologies such as optical ice detection and in-flight emissions measurement, providing an essential platform for accelerating the certification of new technologies.
- Integration of UAVs and autonomous technologies: UAVs and autonomous technologies are redefining air force capabilities, offering more flexible deployment possibilities and enhanced capabilities for air operations. The development of loyal “wingmen”, drones capable of operating in tandem with manned aircraft, shows how the integration of AI and autonomy can enhance combat capabilities without requiring commensurate increases in human or material resources.
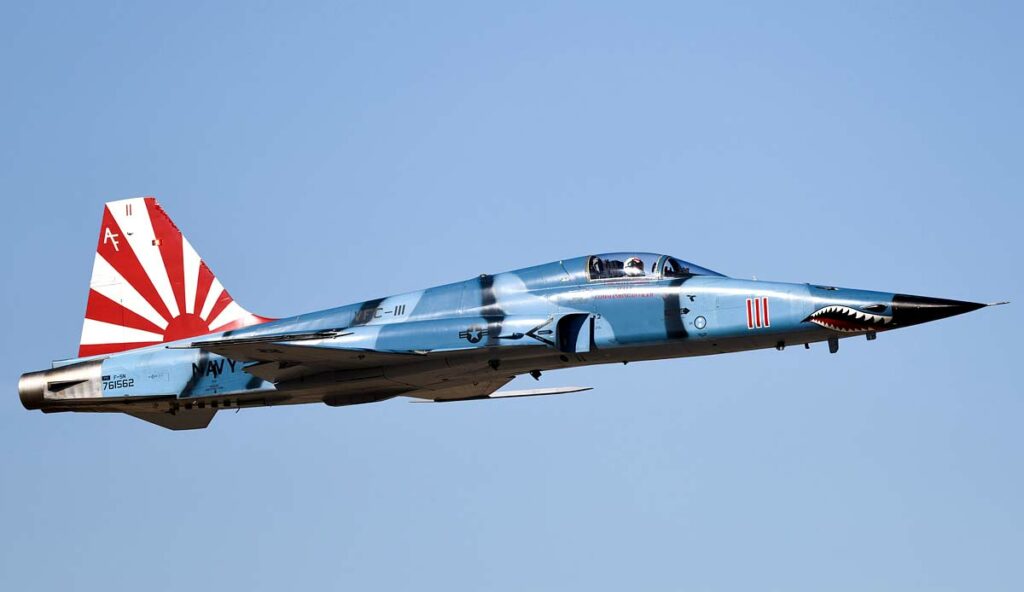
These advances suggest a significant evolution in test procedures for military aircraft, where flexibility, operational efficiency and cost reduction are priorities. With these new technologies, future aircraft testing will be faster, safer and potentially more innovative, enabling rapid adaptation to changing defense and security requirements.
War Wings Daily is an independant magazine.