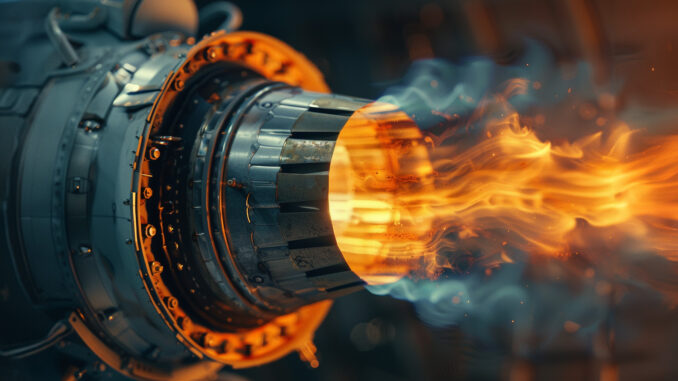
Discover the cutting-edge technologies that improve jet and fighter aircraft propulsion, with a focus on efficiency, power and reduced fuel consumption.
Jet and fighter aircraft propulsion is at the heart of the concerns of aeronautical engineers. The objectives are clear: to increase power while reducing fuel consumption. This article explores innovative technologies and technical improvements that meet these challenges, providing precise technical and scientific information.
1. The development of thermally efficient core engines (HyTEC)
NASA’s HyTEC project aims to reduce the fuel consumption of jet engines by developing a smaller core for turbofan engines. This core reduces the amount of fuel required while maintaining power output. The aim is to improve the overall thermal efficiency of the engine.
Concrete example:
HyTEC incorporates hybridisation, enabling more electrical power to be drawn from the engine, which can then be used to power other systems on board the aircraft. This technology could reduce fuel consumption by 5 to 25%, depending on specific configurations.
2. Rotary detonation engines
Rotary detonation engines represent a significant advance in terms of energy efficiency and power. Unlike traditional engines, these engines use detonation waves to improve fuel combustion, enabling the fuel to be used more efficiently.
Benefits:
- Increases fuel efficiency by 5 to 25%.
- Reduction in engine size and weight, which increases aircraft range without increasing fuel consumption.
Disadvantages:
- Technical challenges related to the injection of fuel and air into the rotating cylinder, requiring advanced numerical modelling solutions.
3. Adaptive engines for fighter aircraft
Adaptive Engine Transition Programmes (ATEP) aim to improve the performance of engines used in fighter aircraft such as the F-35. Adaptive engines adjust their operation in real time according to flight conditions, offering better fuel efficiency and increased power.
Concrete example:
Adaptive engines can offer a 5% improvement in vertical lift power and a 50% improvement in thermal management, which is crucial for high-intensity missions.
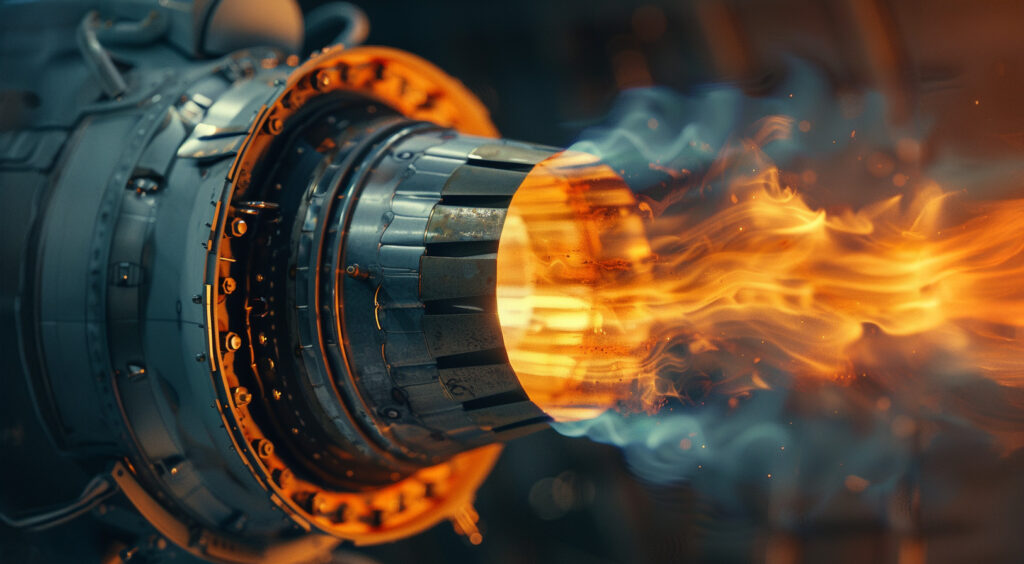
4. The use of advanced materials and aerodynamic designs
The Airbus A350 is a good example of how the use of advanced composite materials and optimised aerodynamic designs can reduce fuel consumption. The A350’s wings are designed to maximise lift and minimise drag, improving overall flight efficiency.
Concrete example:
The A350 uses up to 54% composite materials, which reduces its weight by 20 tonnes compared with previous models. This translates into a significant reduction in fuel consumption and CO2 emissions.
5. Hypersonic combined-cycle engines
Combined-cycle engines, which integrate components from turbine engines and detonation engines, enable hypersonic speeds to be achieved while maintaining high fuel efficiency. These engines can operate like turbojets at low speeds and like scramjets at high speeds.
Benefits:
- Ability to operate at speeds up to Mach 10, offering unrivalled flexibility and power.
- Efficient use of shock and air compression to maximise combustion and propulsion.
Disadvantages:
- Complexity of the transition between propulsion modes and the technical challenges associated with ignition and combustion at supersonic speeds.
Improving jet and fighter propulsion requires a combination of new technologies, advanced materials and innovative aerodynamic designs. Advances in thermally efficient core engines, rotary detonation engines, adaptive engines and hypersonic combined cycle engines promise to make combat aircraft more powerful and more fuel efficient. These innovations offer significant benefits in terms of operational efficiency and reduced emissions, while posing technical challenges that require advanced and continuous solutions.
War Wings Daily is an independant magazine.