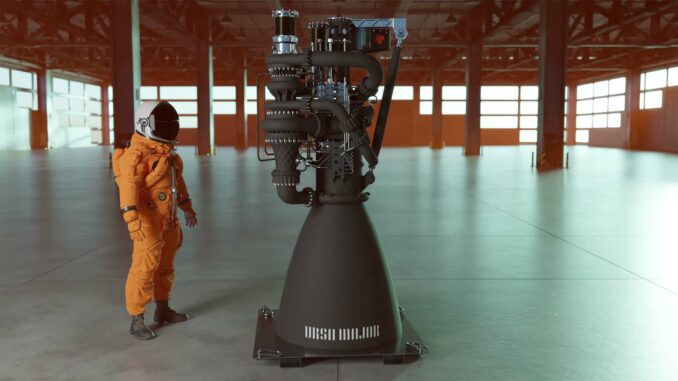
Ursa Major is revolutionizing the production of solid rocket motors using 3D printing, promising faster and cheaper manufacturing. This innovation, dubbed Lynx, could transform the defense industry, improving flexibility and reducing production costs and time, while meeting urgent arms replenishment needs.
Introduction to Ursa Major’s Lynx technology
Ursa Major, a Colorado-based propulsion company, has introduced a revolutionary approach to the design and manufacture of solid rocket motors. Dubbed Lynx, the strategy relies on the use of 3D printing to produce motor casings and subcomponents. Joe Laurienti, the company’s founder and CEO, sees this technology as a way of bringing significant added value to the solid rocket motor sector, traditionally dominated by more conventional manufacturing methods.
The impact of 3D printing on rocket motor production
3D printing offers several advantages in rocket motor production. Firstly, it allows greater flexibility in production, as Ursa Major can quickly switch from one rocket motor model to another without costly retooling. Secondly, it reduces the number of parts required, increases automation and lowers overall costs. For example, some components that were previously manufactured separately and assembled can now be printed in a single piece.
Reduced production time and costs
Lynx can produce around 50 small motor housings, up to 6.35 cm in diameter, in just three days – a task that would take around a month using traditional methods. In addition, Lynx printers can create objects up to 55.88 cm wide, using various metal alloys such as high-strength nickel, titanium and aluminum. This ability to produce quickly and cost-effectively could be crucial in meeting urgent ammunition replenishment needs, such as those generated by the conflict in Ukraine.
Implications for the defense industry
The defense sector, already under pressure due to the limited production chain for solid rocket motors, could benefit considerably from the Lynx approach. In addition to increasing domestic production capacity, this technology could fill production gaps for vital programs such as the Javelin, Stinger and Guided Multiple Rocket Launch System (GMLRS) missiles.
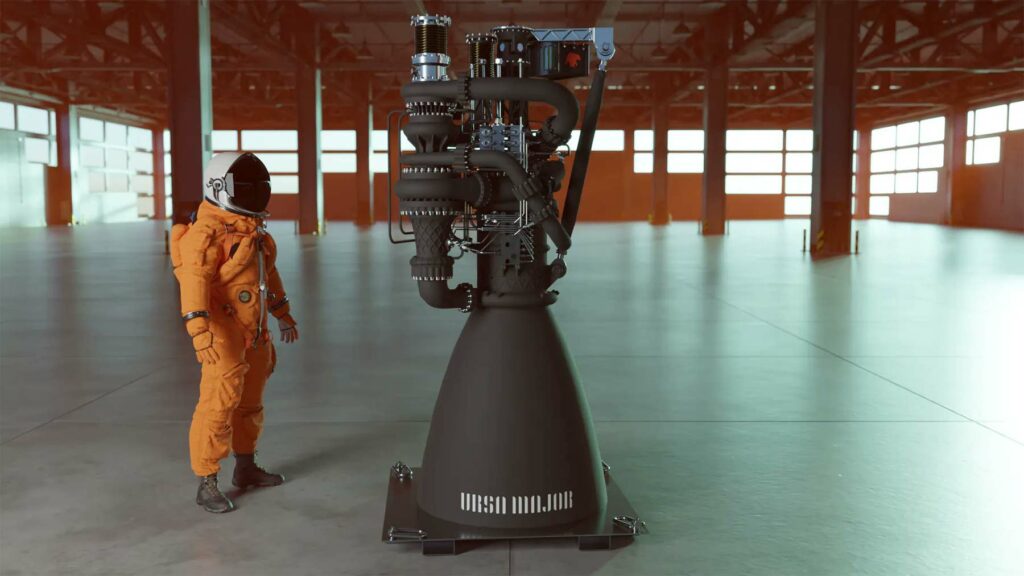
Future plans and expansion of the Lynx approach
Currently, Ursa Major is contracted to use Lynx on one system, with expansion plans to include up to four systems by the end of 2024. Laurienti also plans to have three Lynx 3D printing cells operational within a year. This rapid expansion testifies to the company’s confidence in its technology and its potential to transform the industry.
Long-term consequences of 3D printing adoption
Ursa Major’s adoption of 3D printing could have far-reaching implications for the defense industry and beyond. By reducing production costs and lead times, Lynx could not only meet immediate ammunition needs, but also stimulate innovation in other areas of aerospace technology. It could also encourage other companies to adopt similar production methods, accelerating the move towards more efficient, customizable manufacturing.
Ursa Major’s Lynx initiative represents a major breakthrough in the manufacture of solid rocket motors. By harnessing the capabilities of 3D printing, the company is not only optimizing the production of these essential systems, but could also redefine defense industry standards. By reducing production costs and lead times, this technology could have a profound impact on the way nations manage their defense needs, while paving the way for new innovations in aerospace.
War Wings Daily is an independant magazine.