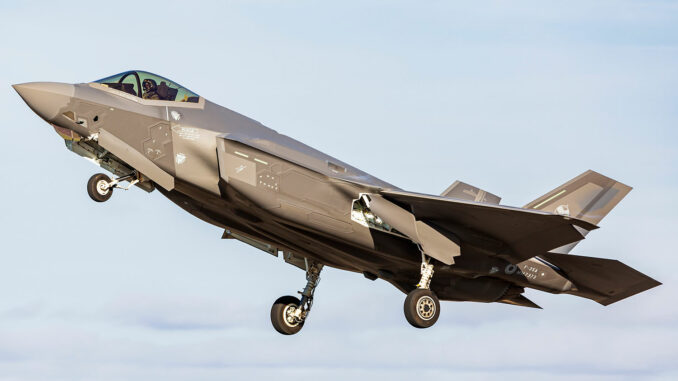
Detailed analysis of the technical and industrial issues encountered during the design of the F-35 Lightning II, an American multirole fighter aircraft.
A complex industrial design from the outset
The F-35 Lightning II program, led by Lockheed Martin, was launched in the early 2000s with a clear objective: to provide a fifth-generation multirole fighter aircraft to several allied air forces. This JSF (Joint Strike Fighter) project was designed to meet the simultaneous needs of the US Air Force, the US Navy and the US Marine Corps, with a common base and specific variants (F-35A, F-35B, F-35C). This approach quickly introduced a major constraint: the standardization of a single airframe for three radically different operational environments.
The first challenge is structural. The F-35B, the short take-off and vertical landing version, requires a Rolls-Royce LiftFan vertical fan system. Integrating this mechanism into a common fuselage has complicated the internal architecture and increased the overall weight of the aircraft. This excess weight has a direct impact on the aerodynamic performance of the other variants. The F-35C, the naval version, has longer wings for landing on a deck, generating additional stress on the landing gear and the airframe.
Stealth has also dictated costly technical choices. The radar-absorbent material (RAM) coating imposes extremely tight assembly tolerances. The carbon composite structure is particularly sensitive to humidity and thermal shock. Millimeter misalignments impact the radar cross-section. The machining of certain parts, such as the leading edges, requires very high-precision 5-axis machines, considerably increasing production costs.
Finally, manufacturing has been hampered by fragmented global logistics. More than 300 suppliers are spread over 11 countries. This dispersion increases delays, quality discrepancies and the difficulty of control. The unit cost of the F-35A, initially expected to be around 50 million USD (46 million €), now exceeds 82 million USD (75 million €), without including long-term maintenance costs.
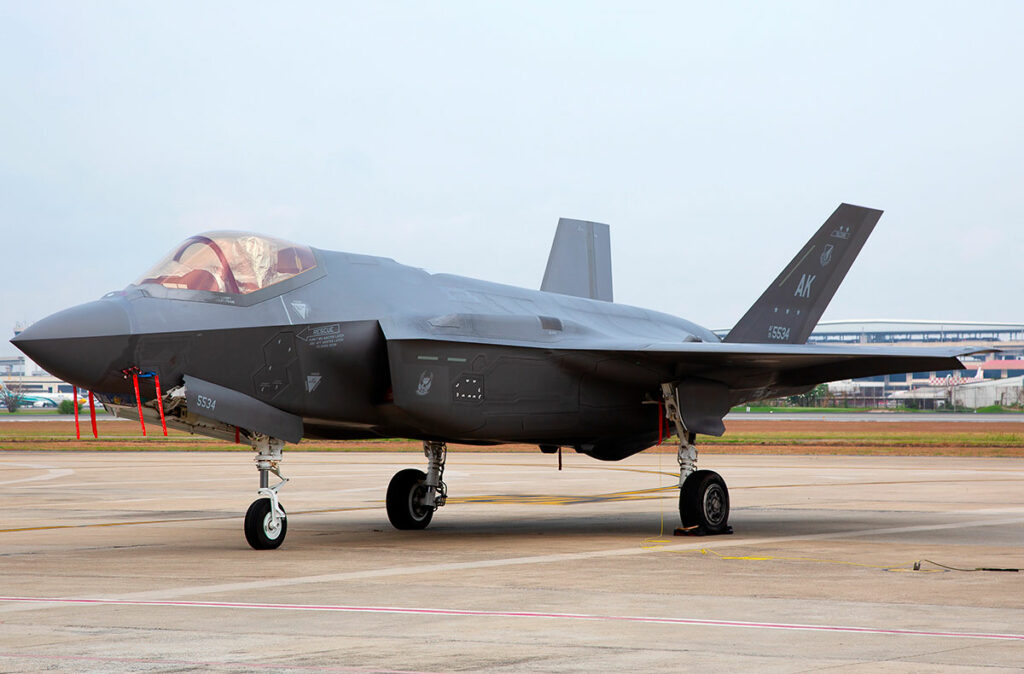
On-board electronics still unstable
The electronic architecture of the F-35 Lightning II was designed as an integrated network, controlled by a centralized software suite called ALIS (Autonomic Logistics Information System), now partially replaced by ODIN. This system was intended to centralize diagnostics, predictive maintenance and mission data. But from the very first years, ALIS showed structural flaws.
ALIS was based on a database that was not synchronized between users, leading to maintenance errors, delays in interventions and configuration incompatibilities. Several US Air Force units reported technical unavailability rates exceeding 20%, with diagnostic errors preventing takeoff. The replacement of ALIS by ODIN has not yet resolved all the malfunctions. In 2023, according to a GAO report, 30% of the ODIN modules installed will not be delivering usable data.
The F-35 carries more than 8 million lines of code. By way of comparison, an F-16 fighter plane has around 2 million. This software overload creates subsystem conflicts, particularly in the AESA AN/APG-81 radar, the ASQ-239 electronic warfare system and the data fusion system. The Block 4 version, still in development, is more than five years behind schedule and requires a partial redesign of the internal processors.
The HMD (Helmet-Mounted Display) helmet, developed by Collins Elbit Systems, has also accumulated defects. The lag in the 3D projection, interface bugs and tracking losses during heavy maneuvers have affected the reading of critical information. These helmets cost 400,000 USD (around 370,000 €) each, and adjusting them requires several hours of configuration by each pilot.
Finally, network connectivity (Link-16, MADL) remains unstable. Interference between aircraft and tactical network saturation in simulated operations limit the level of coordination expected from the F-35 in collaborative combat. This hinders its integration into the multi-domain engagement (MDO) doctrines that the USAF wishes to develop.
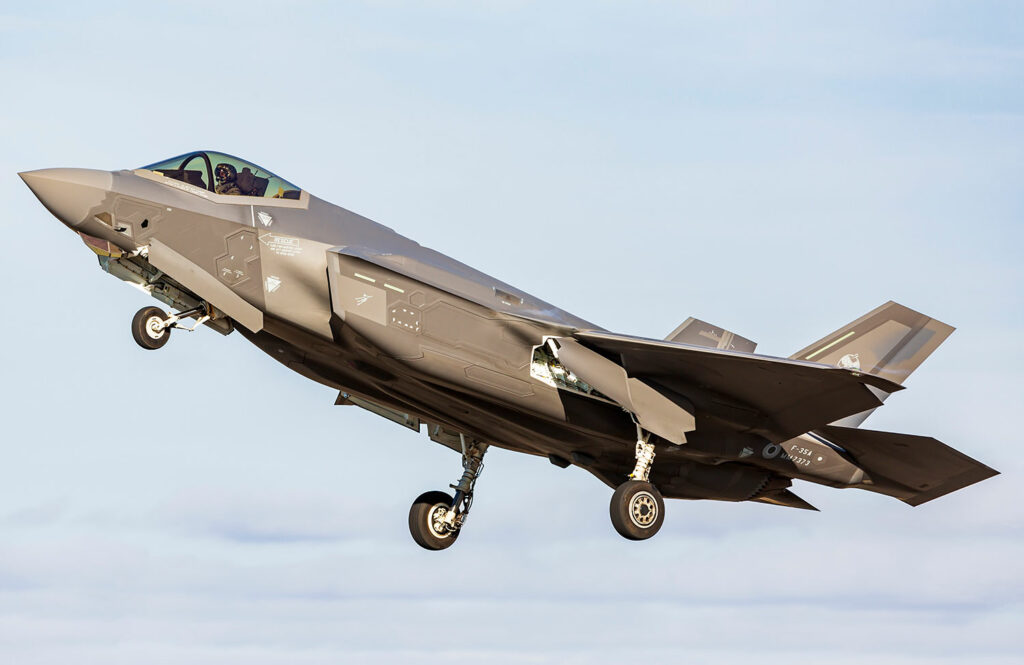
Heavy and costly maintenance in the long term
Beyond initial development, one of the major challenges of the F-35 Lightning II lies in its operational sustainability. The cost per flight hour of the F-35A is currently estimated at 38,000 USD (34,600 €), compared with around 22,000 USD (20,000 €) for an F-16. This inflation is explained by the complexity of the airframe, the fragility of the stealth coating, and the centralized software management.
Each maintenance operation requires precise procedures on RAM materials. The slightest damage to the coating requires repair in a clean room, away from the front line. In 2022, according to DoD figures, more than 45% of the F-35s in the US fleet experienced at least one extended unavailability of more than 30 days.
The Pratt & Whitney F135 engine is also subject to significant constraints. It has an intermediate maintenance rate higher than originally planned. Critical parts such as high-pressure turbine blades require frequent replacement. Several partner countries (Norway, Australia) have reported stockouts of F135 modules, forcing prolonged downtime.
The supply system is slow. The centralization of parts via Lockheed Martin limits the autonomy of the user forces. In France, a Rafale has an average availability rate of over 75%. In the United States, the F-35 struggles to exceed 60% on average.
Finally, the cost of ongoing software modernization, imposed by Lockheed Martin, obliges client states to follow an update cycle every two years. Each software upgrade requires specific adaptations to the simulator and pilot training, extending deadlines and costs.
War Wings Daily is an independant magazine.