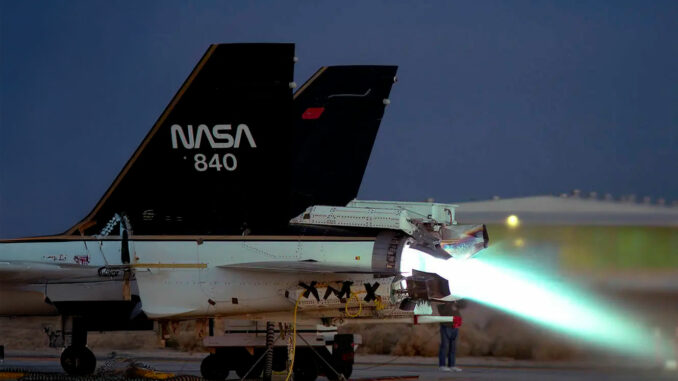
See how a fighter jet optimizes its aerodynamics with fluidic thrust vectoring, reducing the weight of mechanical controls by 20%.
Fluidic control systems replace conventional mechanical control surfaces, such as ailerons or vertical stabilizers, with judiciously directed airflows. Instead of deforming a surface or rotating an external part, they adjust the direction, speed and pressure of the air leaving the engine in real time. This principle is based on the idea that lift and thrust can be modified without imposing additional mechanical constraints, thus reducing the mass and number of elements subject to aerodynamic forces.
Wing Circulation Control, for example, is based on the use of air taken from upstream of the engine’s combustion chamber. This air, generally compressed in the engine’s compression stages, is directed towards fine slots located on the trailing edge of the wing. When this compressed air is expelled at speeds of up to Mach 1.2, it creates a pressure gradient that directly influences lift. In concrete terms, compared with a standard system, conventional ailerons or flaps weigh several tens of kilograms, require hydraulics, actuators, wiring and regular maintenance. Wing Circulation Control, on the other hand, uses an air flow controlled by internal valves. These valves are lighter than moving surfaces and easier to inspect. Precise adjustment of parameters (flow rate, pressure, flow direction) enables fine control of angle of attack, take-off or landing performance, and in-flight stability.
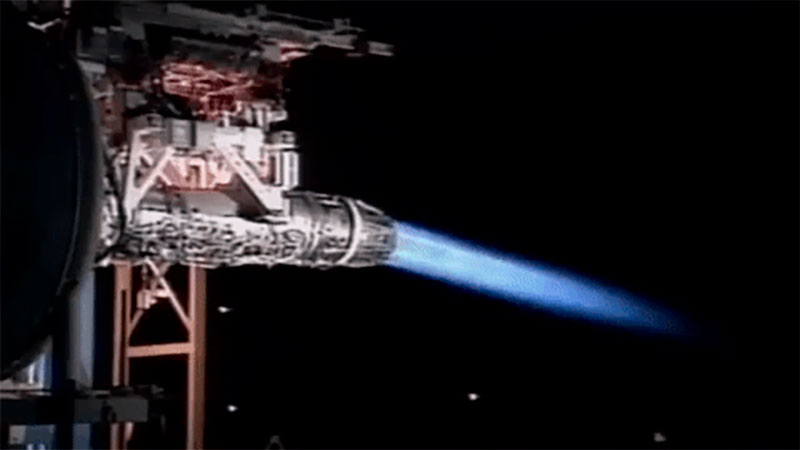
Fluidic thrust vectoring focuses on the engine outlet. Traditionally, thrust vectoring is achieved via movable nozzles, equipped with actuators and mechanical devices. These add weight, drag and maintenance complexity. With fluidic thrust vectoring, all you need to do is inject compressed air into the engine’s output flow. This injection, finely dosed and positioned, modifies the direction of the hot gas jet. Measurements carried out on various test benches show that the thrust vector can be steered through ±15° without the need for external moving parts. This translates into improved manoeuvrability, especially when manoeuvring at high speed or high angle of attack. The pilot (or automated control system) can thus correct a trajectory or accentuate a turn without subjecting the aircraft to significant mechanical stress. The absence of pivoting parts also reduces the costs associated with inspections, component replacement and metal fatigue management. Industry data points to a 10-15% reduction in long-term maintenance costs.
In terms of weight, studies indicate that limiting the use of external surfaces can lighten the aircraft by around 25% in the aerodynamic control segment. For a fighter aircraft weighing several tonnes, this reduction means that it can carry more fuel or operational load, or improve its range. On some missions, fuel savings can amount to several thousand euros per flight hour, depending on the cost of kerosene and the mission profile. In addition, the disappearance of external mechanical appendages reduces the overall surface area exposed to radar detection. Tests have shown a reduction of over 5% in radar cross-sectional area, which contributes to the aircraft’s ability to stay clear of enemy radars. In addition, the absence of external moving parts limits noise emissions, which can be a tactical advantage in operations at intermediate altitudes.
Developing these technologies requires advanced know-how in aerodynamics, fluid mechanics and jet engine design. Flows must remain stable, with rapid response to commands. Wind tunnel tests simulating crosswinds, turbulence and variations in air density are used to optimize these systems before they are integrated into a prototype. Once in actual flight, engineers compare sensor data (pressure, temperature, vibrations, speed, incidence) with those predicted by computer models. Thanks to these analyses, the reliability and efficiency of fluidic control are gradually improved.
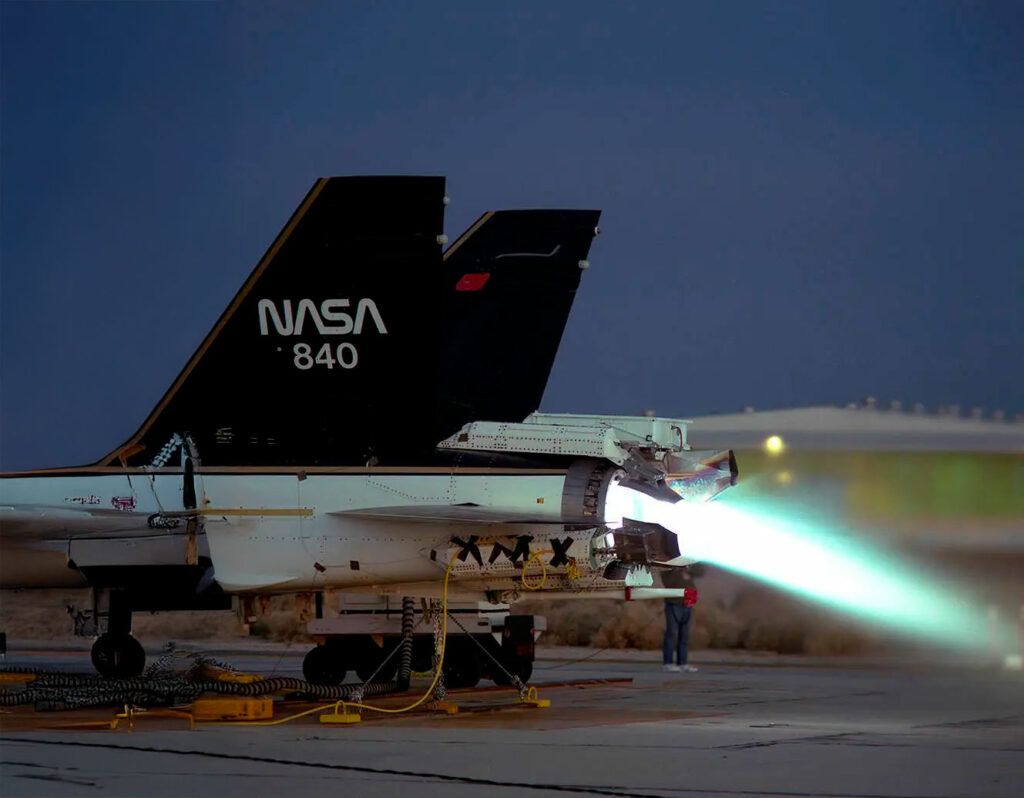
This approach, already tested on a number of experimental aircraft, is attracting the interest of many manufacturers and air forces. They are planning to integrate these fluidic controls into future generations of more powerful, lighter and harder-to-detect aircraft, in order to boost operational efficiency. The adoption of this type of control opens the way to more agile, more responsive aircraft, requiring less maintenance, which meets the strategic and economic challenges of the sector.
War Wings Daily is an independant magazine.