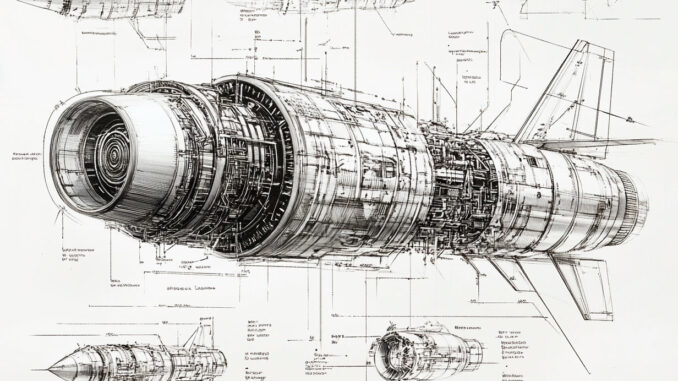
Discover how pulse detonation engines (PDE) are revolutionizing aeronautical propulsion with increased efficiency and reduced emissions.
Pulsed detonation engines (PDE) are attracting growing interest in the field of aeronautical propulsion, due to their potential to offer superior fuel efficiency and reduced pollutant emissions. These engines exploit a unique combustion process based on supersonic detonation waves, offering an alternative to conventional gas turbines. Supported by agencies such as NASA, this technology could transform aerospace propulsion.
PDE operating principles
PDEs operate on a constant-volume combustion cycle that maximizes energy efficiency. Here are the key steps:
- Intake: A precise mixture of fuel and oxygen is introduced into the combustion chamber. For example, NASA experiments have used mixtures of hydrogen and compressed air to optimize homogeneous distribution in the chamber.
- Detonation initiation: An energy source, such as a high-intensity spark or a chemical detonator, triggers a detonation wave. For example, prototype tests have used electrical triggers to ensure stable wave propagation.
- Supersonic propagation : The detonation wave propagates at a speed greater than that of sound (generally between 2,000 and 3,000 m/s), instantly increasing gas pressure and temperature. Tests have shown that this propagation reduces thermodynamic losses compared with deflagration cycles.
- Gas expulsion : Hot, high-pressure gases are expelled at high velocity, generating a direct thrust. In tests on missiles, for example, gas ejection increased their range by 15% compared with conventional turbines.
- Purging and renewal : The chamber is purged to initiate a new cycle. Experimental systems use high-speed valves to prevent combustion residues, improving cycle frequency to several hundred per second.
This cycle is repeated at high frequencies, producing continuous thrust. These principles are currently being tested on high-frequency test benches to verify their suitability for civil and military applications.
PDEs operate thanks to a constant-volume combustion cycle that maximizes energy efficiency. Here are the key steps:
- Admission: A precise mixture of fuel and oxygen is introduced into the combustion chamber.
- Detonation initiation: An energy source, such as a spark, triggers a detonation wave.
- Supersonic propagation: The detonation wave propagates at a speed greater than the speed of sound, instantly increasing gas pressure and temperature.
- Gas expulsion: Hot, high-pressure gases are expelled at high speed, generating the thrust.
- Purging and renewal: The chamber is purged to initiate a new cycle.
This cycle is repeated at high frequency, producing continuous thrust.
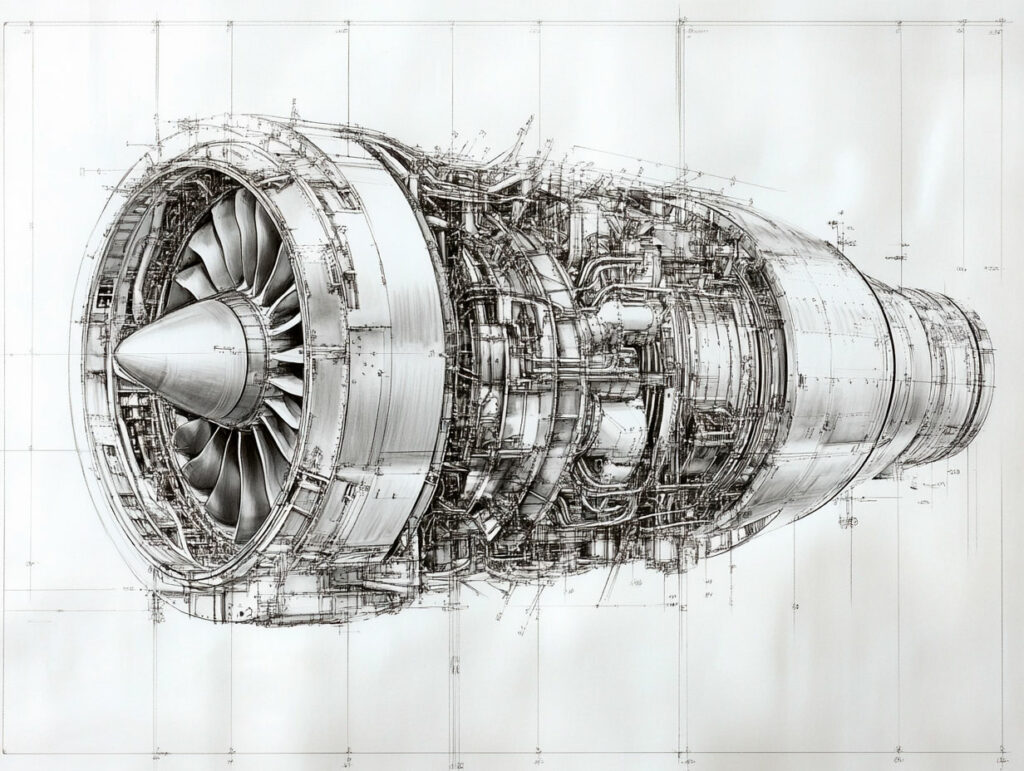
Comparison with gas turbines
Conventional gas turbines rely on constant-pressure combustion, limiting their thermodynamic efficiency. In contrast, PDEs use constant-volume combustion, theoretically 30% more efficient. For example, a conventional turbine converts around 35% of chemical energy into mechanical energy, whereas a PDE can achieve up to 50%. This difference translates into lower fuel consumption for the same thrust.
What’s more, PDEs are mechanically simpler, requiring neither compressors nor rotating turbines. This lowers manufacturing and maintenance costs, offering an attractive alternative in applications such as missiles or drones.
Energy efficiency and reduced emissions
PDEs are distinguished by their ability to deliver increased energy efficiency while reducing pollutant emissions. These engines adopt an innovative approach, combining fast, homogeneous combustion with optimized thermodynamic processes. Here are the main areas for improvement:
- Less nitrogen oxides (NOx) : Combustion in PDEs is not only rapid, but also localized over a very short duration, thus limiting NOx formation. This reduction, estimated at up to 30% compared with conventional engines, is crucial in the context of international environmental standards. For example, a NASA study showed that at hypersonic speeds, PDEs generated significantly less NOx thanks to precise control of combustion parameters.
- Fewer fine particles and unburned hydrocarbons : The uniform combustion of PDEs limits undesirable by-products such as carbon monoxide (CO) and unburnt hydrocarbons. These results are achieved by improving the homogeneity of the fuel-fuel mixture and reducing areas of incomplete combustion in the chamber.
- Compatibility with alternative fuels : PDEs offer exceptional flexibility in the use of alternative fuels such as hydrogen or sustainable aviation fuels (SAF). For example, recent tests have shown that a hydrogen-powered PDE reduces CO2 emissions by up to 80% compared with systems using traditional fossil fuels.
- Increased thermal efficiency: Constant-volume combustion achieves thermal efficiencies of up to 50%, compared with 35% for a conventional gas turbine. This directly reduces fuel consumption, with a commensurate reduction in associated emissions.
The energy efficiency and environmental benefits of PDEs make them a promising solution to the economic and ecological challenges of modern aviation.
EDPs reduce pollutant emissions through faster, more complete combustion. Here are the main environmental benefits:
- Less nitrogen oxides (NOx) : Although detonation produces high temperatures, the very short combustion time limits NOx formation, reducing these emissions by up to 30%.
- Fewer fine particles : Homogeneous combustion minimizes by-products such as carbon monoxide (CO) and unburned hydrocarbons.
- Sustainable fuel compatibility: PDEs can be optimized to run on sustainable aviation fuels (SAF), contributing to greener aviation.
Potential applications
PDEs are being studied for a variety of uses:
- Civil aviation: These engines could be used for small and medium-sized aircraft, reducing operating costs while meeting stringent environmental standards.
- Military aviation: PDEs are ideal for combat aircraft and drones, thanks to their high thrust-to-weight ratio. For example, tests on missiles have demonstrated a 15% increase in range with a PDE engine.
- Space exploration: Their ability to operate efficiently at hypersonic speeds makes them a promising solution for launchers and interplanetary vehicles. NASA is actively studying their use in hybrid systems combining PDE and traditional turbines.
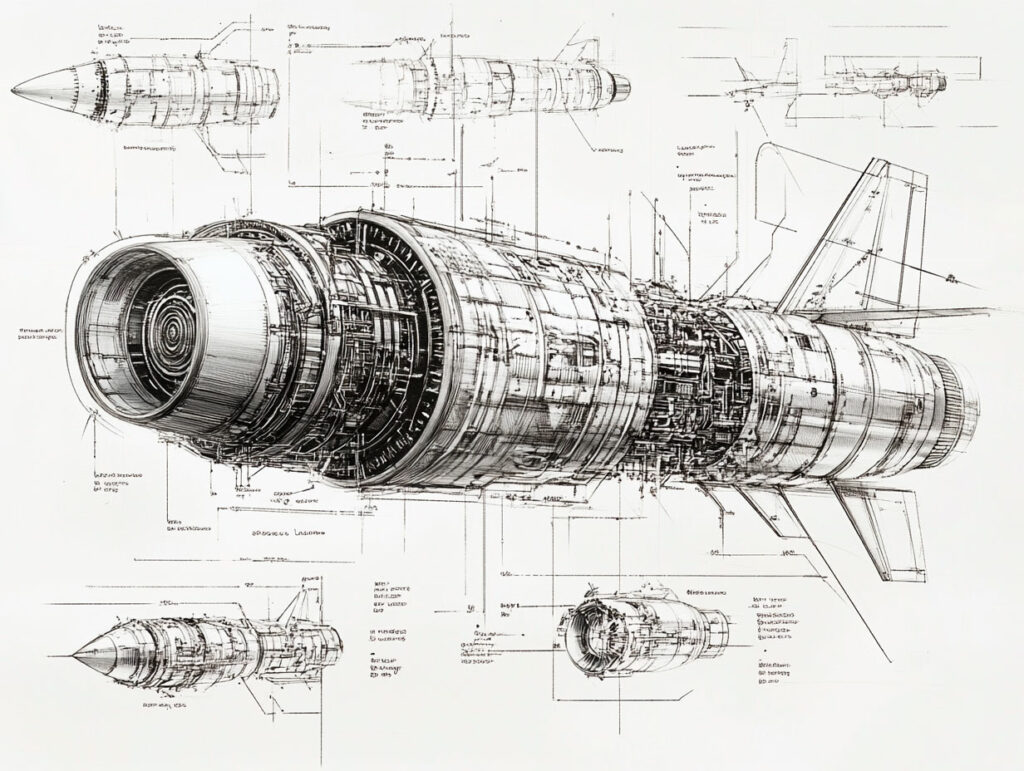
Technical challenges
Despite their potential, PDEs present significant technical challenges:
- Detonation wave control: Maintaining a stable, repeated detonation is complex. For example, irregularities in the fuel mixture can lead to inefficiencies or vibrations.
- Resistant materials: Intense thermal cycling requires materials capable of withstanding pressures of up to several hundred bar and temperatures in excess of 3,000°C. Advanced composites, such as nickel alloys, are currently under development.
- Noise and vibration : PDEs generate high noise levels, posing a problem for civil applications. Adapted silencers and design optimizations are being studied to reduce these effects.
Research initiatives
NASA, in collaboration with industry and universities, is conducting projects to develop functional PDEs. For example, the X-51A Waverider program has tested propulsion concepts based on detonation waves, reaching hypersonic speeds of Mach 5.
Advanced numerical simulations are used to model detonation dynamics and design optimal configurations. In addition, experimental test rigs are used to validate these models and improve performance.
Outlook
PDEs represent an important step towards more efficient and sustainable propulsion systems. Although their widespread adoption requires technical and economic advances, their potential is undeniable in fields such as aviation, space and defense.
With intensive research and continued progress, pulse detonation engines could soon become a reality in modern propulsion systems, meeting the performance and environmental sustainability needs of the 21st century.
War Wings Daily is an independant magazine.